All published articles of this journal are available on ScienceDirect.
Fermentation of Sweet Sorghum Syrup Under Reduced Pressure for Bioethanol Production
Abstract
Background:
Production of bioethanol from sweet sorghum (Sorghum saccharatum) is a promising “green” energy source that can help to reduce energy dependence on petroleum products, to decrease greenhouse gas emissions, and fight environmental pollution. As an additional benefit, it can promote the exploitation of new uncultivated agricultural lands and favor establishing integrated agro-industrial energy independent enterprises. The alcoholic fermentation under reduced pressure may prevent the accumulation of high ethanol concentrations in the cultured broth and thus may create favorable conditions for the highest productivity of yeast Saccharomyces cerevisiae.
Objective:
Elaboration of optimal conditions for sweet sorghum syrup fermentation under reduced pressure.
Aim:
To determine the parameters of sweet sorghum syrup fermentation by S. cerevisiae under the conditions of constant and periodic reduced pressure for the highest bioethanol production efficiency.
Methods:
The sweet sorghum was grown in a temperate continental climate region of Northern Ukraine. The parameters of diluted stem syrup and S. cerevisiae fermentation under reduced and atmospheric pressure were established and controlled by chemical, biochemical and physicochemical methods. The yeast cells were dyed with methylene blue and counted using a microscope and a Neubauer counting chamber. The obtained data have been statistically analyzed.
Results:
It has been established that a periodic vacuum extraction with short-term heating of the medium to the boiling point is the most promising procedure for bioethanol production. Periodically reduced pressure fermentation of sweet sorghum diluted syrup resulted in 55% higher bioethanol productivity compared to atmospheric pressure fermentation. Such treatment enables to maintain the concentration of ethanol in the medium below 5.5% vol., which does not significantly inhibit the productivity of industrial yeast strains and allows adding a nutrient with the subsequent continuation of the cultivation process. The resulting distillate requires less energy for further dehydration.
Conclusion:
The sweet sorghum syrup does not contain substances that inhibit yeast cells although nitrogen and phosphorus supplements are required to support efficient S. cerevisiae growth. The optimal technology, elaborated in this research, consists of repeated cycles of fermentation under reduced pressure (to the level of vacuum) for boiling the cultured broth. This technology provides the highest bioethanol output, high efficiency, and productivity of the overall process.
1. INTRODUCTION
The development of the global economy leads to an augmentation of energy demand. Rapid significant growth of the automotive sector in the recent past has enhanced competition in the global fossil fuels market and its reserved stocks [1]. At the same time, the burning of fossil fuels is one of the significant contributors to global warming due to the high carbon dioxide emissions into the atmosphere. Fuel production from biomass can reduce the negative impact of the energy sector on the environment, ease or eliminate the dependence of many countries on the energy sources import [2].
The first-generation biofuels are mainly produced from rich in sugar and/or starch food crops such as sugarcane or corn but they exacerbate the food vs fuel conflicts. On the contrary, the second generation biofuels are dedicated energy crops that contain lignocellulosic material and are often grown on marginal lands [3-6]. The next-generation biofuel is so far in its early stages of development based on the use of algae as a feedstock [4, 7] or engineered metabolic bacteria as the fuel producers [4]. Although waste-based biofuels produced from lignocelluloses and algal biomass have the potential to eliminate the food to fuel issues, seasonal availability of the first-generation feedstock targeted at a cost-effective production, relatively immature technologies, demanding logistics for sourcing and lack of investments create obstacles to their large scale turnover [8]. Currently, nearly all industrial bioethanol is produced by the first-generation biotechnologies [8, 9].
Sweet sorghum (Sorghum saccharatum (L.) Moench) is a sugar-rich, water-use efficient energy crop. Unlike many other crops, it is fast-growing, highly resistant to pests diseases [10], temperature fluctuations, salinity, and alkalinity of the soils [11-13]. It can be efficiently cultivated on marginal lands [13, 14] with crop rotation systems [14]. Sweet sorghum is considered to be between the first and the second generation biofuel feedstock for the following reasons: (1) it contains simple sugars in the syrup and starch in the seed head, as well as lignocelluloses in the bagasse and leaves [13, 15], and (2) it is not a traditional source for human food in many countries [8, 12, 16]. Co-production of bioethanol along with other biofuels and bioproducts is regarded as a step forward to reduce environmental impact and to increase the economic and energy production effectiveness of biorefineries [8]. Overall, the grain processing products can be used for biodiesel production, while bagasse can also be used for the solid fuel, biohydrogen, biobutanol, biogas production, animal feed, and as a soil fertilizer after composting with other organic wastes [17, 18].
Bioethanol is an alternative to and a potential substitute to petroleum-derived vehicle fuels [19]. Currently, it is the most popular biofuel in the automotive sector [4, 20]. It can be admixed with gasoline in conventional engines at up to 15% whereas flexible-fuel vehicles can use gasoline-ethanol blends containing up to 85% bioethanol [21]. The advantages of using bioethanol include: higher octane number compared to gasoline [4, 12, 20, 22], reduction of greenhouse gas emissions [4, 12], convenience of storage [22, 23] and cleaner exhaust fumes [4].
Fermentation and distillation are the most important technological processes in the production of conventional bioethanol from easily accessible carbohydrates [4, 24], whereas pre-treatment and hydrolysis are essential operations for difficult to degrade lignocellulosic biomass [4, 9] raising the overall production costs [5, 25]. The conventional alcoholic fermentation can be inhibited by high concentrations of its metabolites [26]. Thus, when the ethanol concentration in the fermentation broth grows above 10-12%, the specific ethanol production rate and the specific growth rate of the yeast are heavily suppressed [27-29]. The major targets for the toxicity of ethanol are the plasma membrane and the cytosolic enzymes. Ethanol alters membrane structure and permeability and inactivates and unfolds globular cytosolic enzymes [30-33].
One of the effective ways to overcome ethanol inhibition includes its removal from the fermentation medium as soon as it is generated [34] as well as screening and improvement of microorganism strains, which can be more resistant to alcohol inhibition [31, 34]. Efficient recovery technique of ethanol from the fermentation media is commonly a tradeoff between the recovery rate, costs, and system longevity [24, 35]. As the conventional bioethanol recovery system refers to the distillation process, modified conventional systems comprise the use of vacuum fermentation or additional materials /substances such as membranes, porous adsorbents, gases, and liquid solvents [24].
Pervaporation (abbreviated from ‘permeation’ and ‘evaporation’) is one of the most promising membrane-based separation technologies based on the preferential sorption and diffusion of the target component [36]. The biggest challenge for the equipment performance during the pervaporation separation is fouling, which adds the maintenance costs of repetitive cleaning and causes the problems of contamination due to the growth of bacterial cells on the membrane surface [24]. Gas stripping is the technology for the recovery of alcohols where oxygen-free gas (e.g., N2, CO2 or H2) flows through the fermentation liquor [35]. The drawbacks of such technology include foaming and consumption of large volumes of water [35]. It was also noted [24, 35] that despite CO2 is advised as a fermentation by-product, this gas can be inhibitory to yeast growth. Alcohol removal by liquid-liquid extraction is restricted by the operational difficulties of combining the necessary properties in a single solvent [34].
Generally, membranes are considered costly materials which require maintenance. In turn, solid adsorbents, gas stripping, and liquid solvents demand a subsequent ethanol recovery. At the same time, quick and complete fermentation can be achieved by treating the bioreactor under reduced pressure conditions when bioethanol is continuously extracted from the fermentation broth and condensed using a cooling system [24]. Compared to the conventional bioethanol recovery technique, fermentation and distillation in this process are conducted simultaneously reducing the inhibitory effect of ethanol on the yeast cells.
The aim of the study is to determine the parameters of sweet sorghum syrup fermentation by S. cerevisiae under the conditions of constant and repeated reduced pressure for the highest bioethanol production efficiency. To the best of our knowledge, repeated reduced pressure fermentation has not been previously applied for sweet sorghum stem juice or syrup.
2. MATERIALS AND METHODS
2.1. Preparation of Nutrient Media from Plant Biomass
The seeds of sweet sorghum of the cultivated variety (cv.) Botanichnyi were kindly provided by Prof. D. Rakhmetov, M.M. Gryshko National Botanical Garden at the National Academy of Sciences (NAS) of Ukraine [37]. The S. saccharatum plants were grown in a temperate continental climate zone, Shostka district of Sumy region of Ukraine, situated in the north-east part of the country (51°42′N, 33°12′E, 125 m a.s.l.), within a geographical zone named Polissia. The seeds were planted at the beginning of May, in a soddy podzolic soil, with 45 сm row spacing and 10 cm distance between the plants in a row. The crops were harvested in September after the kernels had matured (Fig. 1A).
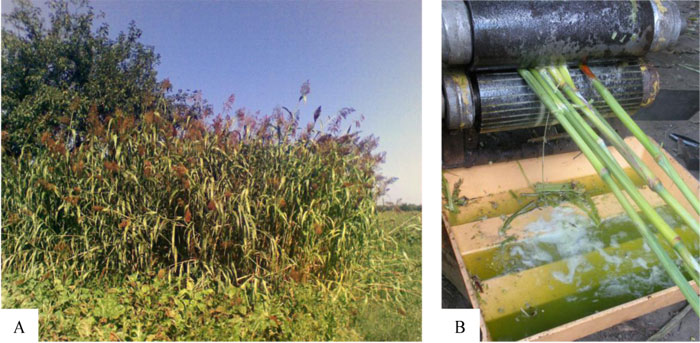
B – squeezed on the roller press.
The harvested sorghum leaves and peeled panicles were squeezed on the roller press producing 1.2 kg of juice out of 3 kg of the biomass. Then, sweet sorghum juice was filtered and concentrated under vacuum in a rotary evaporator at 60±2 °C. The concentrated juice (syrup) was stored at 4 °C. The methods of the chemical analyses are outlined in section 2.3.
Subsequently, the syrup was diluted with tap water to fractions containing 140 g/kg TS, 250 g/kg TS, 400 g/kg TS, autoclaved for 20 min at 121 °C, and used as a yeast growth medium, fermentation medium, and as a substrate for continuous fermentation accordingly. Other components of fermentation media (urea and orthophosphoric acid) were sterilized separately under the same conditions.
2.2. Yeast Strain and Fermentation
S. cerevisiae Meyen ex E.C. Hansen, Medd. Carlsberg Lab.: 29 (1883) Y-М-05 was obtained from the National Collection of Microorganism Strains and Plant Lines for Food and Agricultural Biotechnology of the Institute of Food Biotechnology and Genomics of the National Academy of Sciences of Ukraine. S. cerevisiae Y-M-05 strain was isolated from the surface of millet grain, it is suitable for yeast biomass generation purposes and ethanol production. The stock culture was maintained on 80 g/kg TS barley malt wort agar slants at 4 °C. Barley malt wort was purchased from beer manufacturer Obolon CJSC, Kyiv, Ukraine.
100 g/kg TS sterile barley malt wort was poured into agar slants with malt wort and S. cerevisiae Y-М-05 culture and stored for 3 h at 30 °C. Pre-cultured inoculum liquid was transferred from tubes to 500 ml flask with 300 ml sterile sweet sorghum 140 g/kg TS diluted syrup and cultivated aerobically for 24 h at 30±1 °C on the rotary shaker at 150 rpm. Then, the content of the flask with cultured broth and S. cerevisiae cells was transferred to 3 L Erlenmeyer flask with 1.5 L of 140 g/kg TS diluted syrup and cultivated aerobically at the same conditions as the previous cultivation.
Supplementing the sorghum juice medium with a nitrogen source can stimulate yeast cell growth and ethanol production [38]. For this reason, 0.33 g/kg or 0.64 g/kg urea was added to sweet sorghum diluted syrup. The control syrup had no urea added. For this experiment, 500 ml Erlenmeyer flasks with 300 ml of 140 g/kg TS sterile sorghum syrup were inoculated with 30 ml of seed culture and incubated at aerobic conditions for 12 h at 30±1 °C on the rotary shaker at 150 rpm.
Seed culture for bioethanol production was prepared in five 3 L Erlenmeyer flasks with 1.5 L of 140 g/kg TS sterile sorghum syrup and 300 ml inoculum, cultivated aerobically at 30±1 °C on the rotary shaker at 150 rpm. The selected amount of urea (0.33 g/kg) and 0.09 g/kg of 70% orthophosphoric acid were added to the syrup as a source of phosphorus to facilitate the biomass accumulation and to increase the ethanol output [38, 39]. When Brix of the fermentation broth decreased twofold at the exponential yeast growth phase, 15 ml of the inoculum was transferred to 1 L Erlenmeyer flask with 600 ml working volume comprising: sorghum 250 g/kg TS diluted syrup with 15 drops of Antifoam FD 20 PK for the anaerobic phase of alcoholic fermentation. Initial pH was maintained at 4.7 with 1 N sulfuric acid.
The general diagram of conducting the sorghum diluted syrup fermentation in flasks is shown in Fig. (2). Control fermentations were performed at atmospheric pressure, while two test treatments were conducted after 18th h of fermentation to allow ethanol to accumulate in the cultured milieu. The treatment (1) consisted of 10 min periods at 20±5 mmHg reduced pressure and the treatment (2) was delivered at a constant 80±5 mmHg pressure throughout the fermentation period.
All flasks were placed on heated magnetic stirrers ММ3M (Mukachiv Factory Complete Laboratories JSC, Ukraine). The flasks under atmospheric pressure were closed with rubber stoppers containing two holes each for the thermometer and hydraulic seal.
To carry out the part of the experiment under reduced pressure (Fig. 2), the flasks were connected through a Vyurtz nozzle with a thermometer and Liebig condenser (500 mm length). On the other side, the condenser was joined to a receiving flask via an allonge for vacuum extraction. The round-bottom receiving flask was immersed in a container with ice. The vacuum pressure was maintained using a water jet pump generating a vacuum of maximum 10-20 mmHg, pumping speed of 0.15 L / sec. The water jet pump was connected via a vacuum meter and a tee to the allonge. The tee was used to control the vacuum and to stabilize the system for a long time under the relatively constant vacuum. The vacuum level was measured using a laboratory mercury vacuum meter. Yeast cells were dyed with methylene blue and counted with a Neubauer haemocytometer [40], using a JENAVAL optical microscope (Carl Zeiss, Germany).
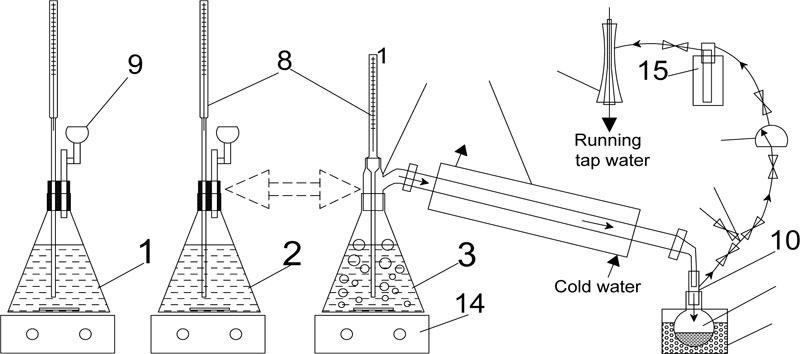
To scale up the process, a 5 L fermenter was used, (Fig. 3). The inoculum preparation for fermentation in the bioreactor was the same as for reduced pressure experiment in flasks. The adaptation of inoculum was performed in the fermenter for 2 h at 30±1 °C. Yeast seeds (20 g/L) were placed into a 2 L displacement filled with 140 g/kg TS sorghum syrup supplemented with 0.33 g/kg urea and 0.09 g/kg of 70% orthophosphoric acid. Yeast adaptation and growth took place in aerobic conditions by bubbling filtered air through at 3 L/L, with a compressor. For yeast growth at atmospheric conditions, a hydraulic seal was used.
Bioethanol production was performed in a 5 L fermenter with 250 g/kg TS sorghum syrup, pH 4.7 was adjusted with 1 N sulfuric acid, in anaerobic conditions at 30±1 °C. The vacuum extraction was conducted at 20±5 mmHg for the separate 1.25 L fractions of the medium in 2 L Erlenmeyer flasks for 8 min. Following the extraction, the content of the flask was returned to the bioreactor for further fermentation.
2.3. Establishment of Sweet Sorghum Syrup and Fermentation Parameters
The parameters of sweet sorghum syrup, including moisture (water and TS content), ash, pH, titratable acidity were determined according to the AOAC methods [41]. To analyze the water content, the samples were dried at 105 ºC until constant weight [42]. The ash content was established by incineration at 600 ºC until constant weight [42]. The pH value was checked with pH meter millivoltmeter pH-150-M model (Gomel Plant of Measuring Devices, the Republic of Belarus) standardized against standard buffer solutions.
The content of reducing sugars was analyzed by Lane and Eynon method (ISO 5377:1981) by titration the sample to a Fehling's solution with methylene blue as an internal indicator. The total sugars (reducing sugars + sucrose) content was analyzed by Lane and Eynon method after the inversion of sucrose with hydrochloric acid at 69±1 °C. Alternatively, digestible carbohydrate content was tested by the biological fermentation method (GOST 31683-2012).
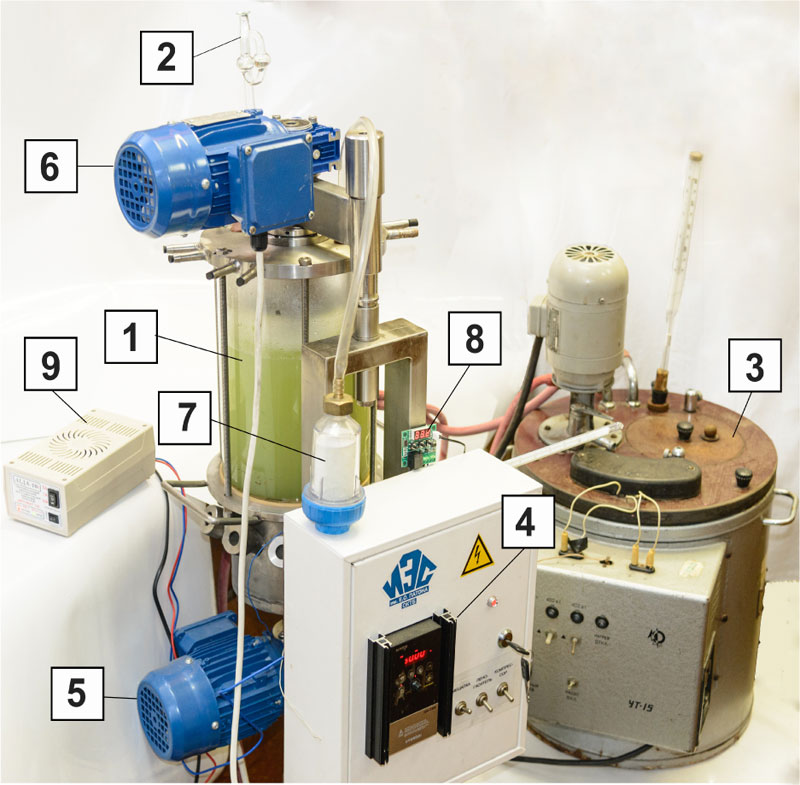
Calcium content in sweet sorghum syrup was determined by EDTA complexometric titration method [43]. The nitrate content was evaluated by the titrimetric method after the reduction to ammonia under alkaline conditions with Devarda’s alloy as the reducing agent [44]. The nitrogen content was defined by Kjelhdal’s method after titration of distilled ammonia with K2SO4 and CuO used as catalysts for acid mineralization at 1.4±0.14 kW heating electrical power in UDC-7 mineralizer (Spectro Lab LTD, Ukraine) [45]. The total phosphorus content was tested in the ash [46] by the colorimetric Brigg’s method [47].
The fermentation process was monitored via analysis of the alcohol content in the distilled samples and measuring the Brix of the medium and broth using saccharometer AC-3 (Shatlyhin & Co LTD, Ukraine). Following the extraction of volatile substances and water vapor, the Brix value of the distillery sludge was measured after adjusting it to the volume of the culture liquid sample. Undigested sugars in mature culture liquid were determined by the colorimetric micro method with resorcinol [48] using the Concentration Photoelectric Photometer model KFK-3-01 (Zagorsk Optical-Mechanical Plant, Russia).
The bioethanol yield (YP/S) was calculated [49] as the actual ethanol produced and expressed as the weight to weight ratio, g ethanol per g total sugar utilized (g/g). The bioethanol productivity (Qp, g L-1 h-1) and the conversion efficiency of bioethanol yield (Ey, %) were calculated by the following equation [49]:
![]() |
where P – the actual bioethanol concentration produced (g L-1), t – the fermentation time (h) and 0.54 is the maximum theoretical bioethanol yield of sucrose consumption.
2.4. Statistical Analysis
All measurements have been done in triplicates and the data presented are the mean values of three independent experiments expressed as mean ± errors. The data have been statistically analyzed by t-test using Origin 2016, OriginLab Corporation, USA. Differences between means at 5% (p < 0.05) level have been considered significant.
3. RESULTS AND DISCUSSION
3.1. Sweet Sorghum Yield and Yeast Growth
The sorghum biomass yield at the time of harvest in the ripen seeds vegetation phase reached 92 t/ha, the stem juice yield was 36.8 t/ha, 14 °Brix, 99.5 g/kg of fermented carbohydrates. As was previously reported by Widianto et al. [50], sweet-stalk sorghum juice does not contain substances inhibiting yeast growth, which is testified with the lag phase duration similar to the standard medium. The main fermentable sugars in sorghum juice are sucrose, glucose, and fructose [29, 50, 51]. Fructose is mostly utilized as the last option [50]. In the tested sample of sweet sorghum syrup, sucrose accounted for approximately 68% of fermented sugars and the reducing sugar share amounted to 32% of the total fermented sugars output (Table 1), which matches the literature (65-68% sucrose, 17-22% glucose, 12-15% fructose) [52]. The differences in sugar content and variations in their distribution in the sorghum juice might be attributable to the impact of environmental factors, managing practices, soil properties [52], and to a large extent, to different sorghum varieties [17]. A linear relationship was established between the total sugar content in the sorghum juice and Brix data, which can be convenient to estimate the potential ethanol output of the raw source by the field analytical test [17].
Appropriate nutritional conditions such as sufficient nitrogen levels in accessible form affect the adaptation of S. cerevisiae cells to higher ethanol concentrations [53]. Davila-Gomez et al. showed [11] that concentration of soluble nitrogen-containing compounds in sorghum juice depends on the variety, but is generally below the level, required for structural and enzymatic protein synthesis in S. cerevisiae, hence nitrogen supplementation should be necessary for quality sustainable fermentation. The most efficient nitrogen sources for bioethanol production are ammonium sulfate and urea [20]. Yue et al. showed [54] that adding urea to sweet sorghum helped in the growth of maximum ethanol concentration in the broth as well as increased the number of yeast cells. In contrast, ammonium sulfate did not show positive effects. Previous studies have shown that urea, added as a nitrogen source, protects the yeast from osmotic stress [38, 55], and acts as a molecular filter binding to proteins and preventing their destruction during alcohol production [30, 55].
Parameter | Unit | Value |
---|---|---|
Water content | g/kg | 238.1 ± 40.0 |
Total solids (TS) | g/kg | 761.9 ± 40.0 |
Ash | g/kg | 39.2 ± 1.0 |
рН | dimensionless | 4.13 ± 0.10 |
Acidity | degree | 0.30 ± 0.01 |
Reducing sugars | g/kg | 162.3 ± 10.0 |
Total sugar (reducing sugars+sucrose) | g/kg | 510.6 ± 30.0 * |
Fermented carbohydrates | g/kg | 540.9 ± 43.8 * |
Calcium | g/kg | 1.63 ± 0.08 |
Nitrates | g/kg | 1.51 ± 0.05 |
Total nitrogen | g/kg | 3.50 ± 0.10 |
Phosphorus (normalized by Р2O5) | g/kg | 0.2202 ± 0.0110 |
The effect of urea addition on sugar utilization is shown in Fig. (4). Adding urea significantly impacted the degradation of medium components starting from the 5th h of yeast cultivation. Control values started to drop slowly from 5th to 7th h which can be attributed to the adaptation of yeast cells to urea supplementation. When Brix of the supplemented fermentation broth decreased two-fold, the addition of 0.33 g/kg and 0.64 g/kg urea caused practically no significant differences in the fermentation efficiency in sweet sorghum syrup medium.
о – the control means and test values are not significantly different (p < 0.05);
+ – the control means and test values are significantly different (p < 0.05);
* – the control means are significantly different compared to test values (p < 0.05), and test values are not significantly different (p < 0.05).
The data in Fig. (4) shows that adding 0.33 g urea to 1 kg of diluted 140 g/kg TS syrup (0.15 g/kg nitrogen) provided the best result while further increase of urea supplementation did not lead to a significant reduction in dissolved solids in the medium, which is consistent with prior research [39]. However, in the case of very high gravity (VHG) due to adding extra sugar to the sorghum juice, or when the concentrated juice contains over 270 g/L TS [53], much greater supplementation of urea is required [38, 56].
3.2. Fermentation of Sweet Sorghum Diluted Syrup in Flasks Under Reduced and Atmospheric Pressure
Parameters of fermentation processes under reduced pressure depend on the physical properties of the ethanol-water mixture and the biochemical properties of the yeast fermentation process [57].
In this experiment, under the lowest pressure conditions, the ethanol concentration in the broth at the end of the fermentation reached maximum 5.4% vol. while this parameter under atmospheric pressure produced 11% vol. ethanol (Fig. 5B). Higher alcohol content was obtained in glucose-yeast-peptone fermentation by S. cerevisiae: 6.33% vol. ethanol in a flask under 47 mmHg pressure and 14.75% vol. under atmospheric pressure conditions [57]. Although 10-12% of ethanol concentration strongly depresses the specific ethanol generation rate and the specific growth rate of the yeast cells [27-29], significant metabolite changes can be observed at 5% vol [58].
The lower concentration of ethanol in flasks under vacuum conditions resulted in substantial bioethanol productivity compared to control under atmospheric pressure: 22% higher under constant reduced pressure and 55% higher under periodic reduced pressure (Table 2). Periodic reduced pressure allowed the fermentation medium to boil periodically which resulted in significantly higher (33%) ethanol extraction. The Brix parameter was also the highest in periodic reduced pressure mode, (Fig. 5A, C) for the reason of boiling-off the water vapor and a higher concentration of cultured broth. At the same time, the residual undigested sugars in mature cultured broth were 65% higher at atmospheric pressure compared to periodic pressure treatment (Table 2).
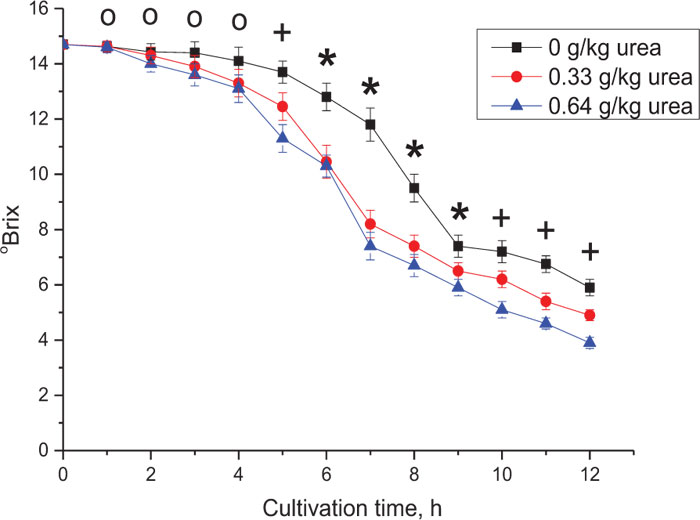
The process of bioethanol production can be prolonged and enhanced by applying the reduced pressure fermentation approach and with the addition of more feeding, since the inhibiting concentrations of ethanol in cultured broth are accumulated slower than under atmospheric fermentation. We performed two additional feedings in fermentations with a reduced pressure approach (Fig. 5A), which resulted in the increase of Brix (Fig. 5A, C). After the second feeding, ethanol concentration decreased due to dilution with a new portion of medium (Fig. 5B). In the case of fermentation under atmospheric pressure, only one additional feeding was applied (Fig. 5A).
Fermentation mode | Yeast cell concentration, ×108 cells/ml | Undigested sugars in mature cultured liquid, g/L | Bioethanol yield (Yp/s, g/g) | Efficiency of bioethanol yield (Ey, %) | Bioethanol productivity (Qp, g×L-1 h-1) |
---|---|---|---|---|---|
Constant reduced pressure at 80±5 mmHg | 3.3 ± 0.1 a | 2.52 ± 0.07 a | 0.50 a | 92.6 a | 1.18 a |
Periodic reduced pressure at 20±5 mmHg | 3.6 ± 0.1 b | 1.83 ± 0.04 b | 0.53 b | 98.78 b | 1.50 b |
Atmospheric pressure | 3.8 ± 0.1 b | 3.02 ± 0.08 c | 0.49 a | 91.37 c | 0.97 c |
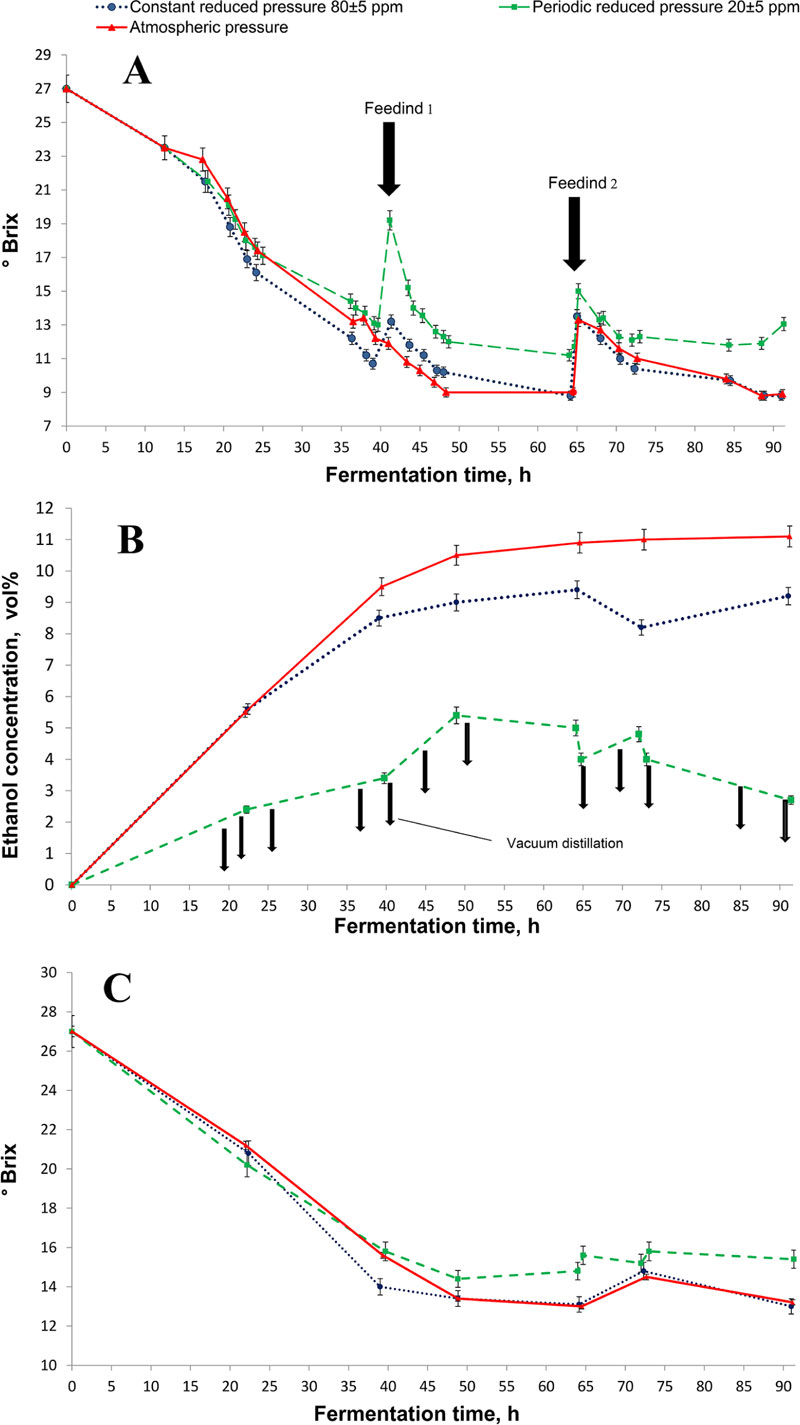
According to Samnuknit and Boontawan [59], in the case of extractive fermentation under reduced pressure, feeding supplementation can be repeated up to 9 times with the same inoculum of yeast. However, after that, yeast cell viability weakened presumably due to the accumulation of approximately 70 g/L of lactic acid. We believe that the accumulation of non-volatile metabolites can be further limited by cultural liquid output as was also suggested by literature data [60].
It is generally accepted that fermentation conditions affect yeast cell viability and reproduction capacity. As demonstrated by Xie et al. [61], fermentation under reduced pressure can inhibit yeast reproduction although the ethanol productivity gets enhanced. However, our data show that pressure does not particularly affect pH: while the initial pH was 4.7, the final pH after fermentation was 4.7±0.1 and 4.8±0.1 under reduced and atmospheric pressure, respectively.
In the case of ethanol fermentation under vacuum, yeast cells suffer oxygen deficiency stress, intracellular and extracellular pressure difference, and accumulation of non-volatile toxic metabolites [62]. Prior to comprehensive analyses of proteomic [63] and lipidomic [64], adaptive responses of S. cerevisiae to repeated vacuum fermentation explain the higher viability of cells compared to the same parameter under constant reduced pressure conditions.
As presented in Table 2, the highest bioethanol output, efficiency and productivity of the process were received with periodically reduced pressure fermentation at the level of vacuum close to the boiling point of the cultured broth. At the same time, this mode did not significantly affect the final yeast cell concentration that allowed a more complete utilization of the sorghum syrup sugars (Table 2). The maximal ethanol output was received when its concentration was below 5.5% vol (Fig. 5B).
The fermentation process of the yeast occurs at the temperature 30-35 °C. Depending on the ethanol-water concentration, the mixture boils within the range from 78.3°C up to 100°C [57]. When the fermentation process takes place under reduced pressure, the boiling point of this mixture also decreases. The main feature of volatile components separation from the alcohol mash is the possibility of boiling the cultured liquid under reduced pressure and the temperature of fermentation 30-40 °C. The advantage of fermentation under reduced pressure is the possibility to minimize the inhibition of the producer by volatile products of metabolism. Nevertheless, a thorough technical and financial analysis of the reduced pressure fermentation technology is required before a decision can be made on its practical industrial application.
3.3. Fermentation of Sweet Sorghum Syrup in a Bioreactor with Periodic Vacuum Extraction of Cultured Broth Fractions
These scaling up experiments were performed in a continuous stirred 5 L tank reactor (CSTR) (Fig. 3). It allowed to increase the volume more than 8 times (from 600 ml working volume in the flask), automatic control of the temperature, aeration and defoaming as well as stirring throughout the fermentation. Periodic vacuum extraction of a quarter of the cultured broth at 20±5 mmHg was conducted as shown in Fig. (6). This treatment helped to maintain the ethanol concentration in the broth at 5.2% vol. prior to distillation and enabled feeding with 160 ml portions of 400 g/kg TS sorghum syrup as shown in Fig. (7).
The parameters of yeast survival rate, undigested sugars of cultured liquid, and bioethanol yield in the bioreactor were similar to those under periodic vacuum extraction in the flasks even though the medium was subjected to the reduced pressure only partially. This performance has been achieved due to a quality mass transfer in the bioreactor. The distillate obtained in the cold trap had an alcohol concentration of about 32% vol. and needed less energy for further dehydration than ethanol produced in the bioreactor. Such a positive feature of the bioethanol fermentation under reduced pressure was also reported by Nguyen et al. [57].
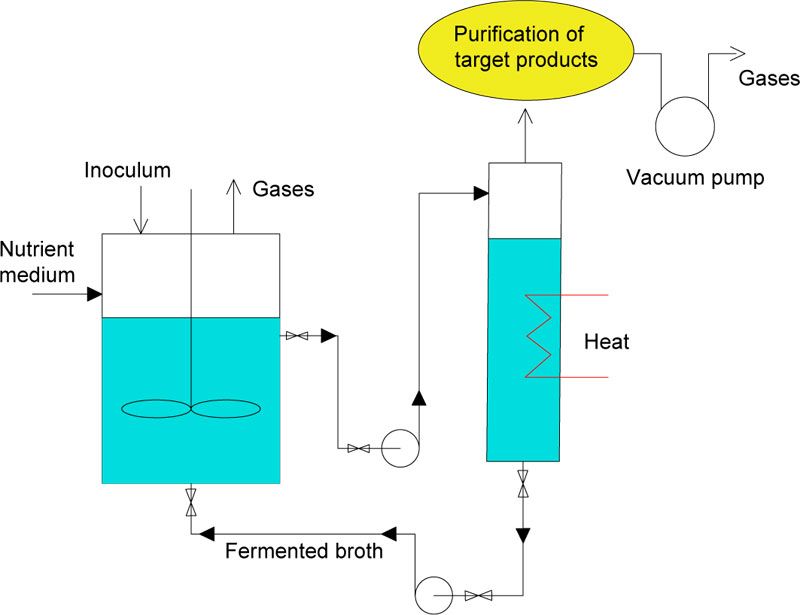
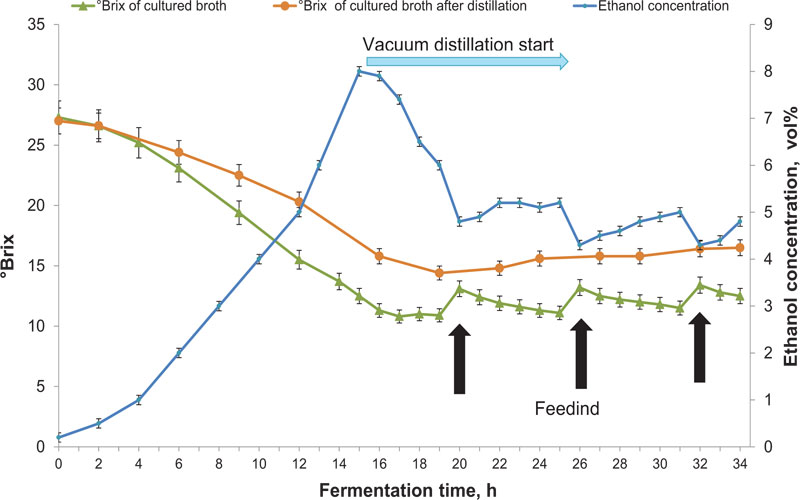
When creating a vacuum for the entire volume of the fermenter, its production rises in price because of the need for thick walls. To overcome such restrictions, fermentation under the atmospheric pressure, and vacuum extraction of broth portions in a separate fermentation tank (flash fermentation) was carried out and proposed for further implementation. The technology layout illustrated in Fig. (6) is suitable for implementation on bioethanol plants. It has the potential to increase the productivity due to avoiding inhibition of yeasts by high alcohol concentrations, the gradual feeding of additional sugar source and a prolonged use of the yeast biomass in the active growth phase via continuous extraction of volatile metabolites. VHG approach with high initial concentrations of sugars can also be performed with ethanol extraction at least from a part of the cultured liquid [60].
CONCLUSION
The sweet sorghum syrup does not contain substances that inhibit yeast cells although nitrogen and phosphorus supplements are required to support efficient S. cerevisiae growth. The optimal technology, elaborated in this research, consists of repeated cycles of fermentation under reduced pressure (to the level of vacuum) for boiling the cultured broth. This technology provides the highest bioethanol output, high efficiency, and productivity of the overall process.
LIST OF ABBREVIATIONS
CSTR | = Continuous stirred tank reactor |
cv | = cultivated variety |
EDTA | = Ethylenediaminetetraacetic acid |
m.a.s.l. | = metres above mean sea level |
NAS | = National Academy of Sciences |
TS | = Total Solids |
VHG | = Very high gravity |
ETHICAL APPROVAL AND CONSENT TO PARTICIPATE
Not Applicable.
HUMAN AND ANIMAL RIGHTS
No animals/humans were used for studies that are the basis of this research.
CONSENT FOR PUBLICATION
Not applicable.
AVAILABILITY OF DATA AND MATERIALS
The authors confirm that the data supporting the findings of this study are available within the article.
FUNDING
This work was supported by the National Academy of Sciences of Ukraine (Project No. 0114U002171).
CONFLICT OF INTEREST
The authors declare no conflict of interest, financial or otherwise.
ACKNOWLEDGEMENTS
We acknowledge the suggestions of Dr. V. Kyrylenko (Institute of Food Biotechnology and Genomics, National Academy of Sciences of Ukraine, Kyiv) to improve the language of the manuscript. Also, we acknowledge the work of design engineer Volodimir Kryvonos (State Scientific-Research Institute of Chemical Products, Shostka, Sumy Oblast, Ukraine) on the construction of the roller press for squeezing sweet sorghum juice.