All published articles of this journal are available on ScienceDirect.
High Efficiency of Food Waste Fermentation and Biohydrogen Production in Experimental-industrial Anaerobic Batch Reactor
Abstract
Background:
Multicomponent organic waste is a significant environment hazard. Natural mechanisms can no longer ensure the processing of increasing volumes of such waste. The accumulation of multicomponent organic waste to environment pollution with toxic gases and leachate. Therefore, there is an urgent need to develop cost-effective technologies for the rapid treatment of huge volumes of toxic waste. Moreover, multicomponent organic waste can be used as the substrate for the production of green energy - biohydrogen.
Objective:
To scale up the technology of biohydrogen production from multicomponent organic waste in experimental-industrial anaerobic batch reactor and to establish fermentation parameters of its operation.
Methods:
An experimental-industrial anaerobic batch reactor was designed and the method of thermodynamic prognosis was applied to determine the most effective microbial pathway for hydrogen synthesis. The efficiency of the fermentation was evaluated by the pH and redox potential (Eh, mV) of culture medium, the concentration and volume of synthesized gas.
Results:
The experimental-industrial anaerobic batch reactor with a volume of 240 L was successfully applied to scale up the process of obtaining hydrogen via fermentation of organics. The duration of the technological cycle (T) was 1.5-4 days. The coefficient of waste destruction (Kd) that is the ratio between the initial and final weight of waste was high and ranged from 86 to 140. Hydrogen yield was 45-90 L/kg of dry weight of waste. The maximum concentration of hydrogen (H2max) was 50-58%.
Conclusion:
The developed approach and scaling of the biotechnology is promising for industrial application for effective hydrogen production via dark fermentation of multicomponent organic waste. Its industrial application might help to solve the problem of toxic multicomponent organic waste destruction and simultaneously to produce green energy H2.
1. INTRODUCTION
Today, two strategically important problems are being faced by the mankind. The first one is the continuous growth of volumes of multicomponent organic waste [1-3]. The second problem is the necessity of obtaining renewable energy sources [4-10]. Rapid accumulation of Multicomponent Food Waste (MCFW) occurs both in developed countries [5] and in developing ones [11-14]. The amount of organic waste increased up to 4 times during last decades [15]. Additionally, to direct losses of food and land resources in landfills as well as environment pollution, by products of uncontrolled decay of MCFW, about 3 billion tons of CO2 (greenhouse gas) is released annually to the atmosphere [16-21]. Fossil energy sources (natural gas, coal, oil) are continuously exhausted, therefore, there is a problem of providing energy needs in future [22-29].
The development of effective biotechnologies for fermentation of organics is the promising solution of both of these strategically important problems. Such biotechnologies will provide fast degradation of organic waste with simultaneous obtaining of green energy H2 [7, 30-33]. Multicomponent food waste is promissing for H2 production via anaerobic degradation. It has the following advantages for fermentation: moisture content (72-85%), high substrate concentration - up to 346 g/L via Chemical Oxygen Demand (COD) including up to 143 g/L carbohydrate, and high carbon to nitrogen (C:N) ratio (9:21) [34].
Different strategies have been proposed for the decomposition of multicomponent organic waste. The United States and countries of the European Union are world leaders in the utilization of household organic waste. Household food waste is utilized with biohumus production in the United States. In the United Kingdom, organic waste is processed by methane fermentation. Obtained biogas is used as fuel for municipal transport. In the Eropean Union, food and agricultural waste is also digested in methane tanks. However, now biogas technologies are considered to be a temporary method of solving the problem of utilization of food waste, because they do not provide efficient utilization of waste and economically advantageous biogas synthesis [35-38].
The development of biotechnologies for the destruction of organics with the synthesis of molecular hydrogen is the most promising pathway. Among the different energy carriers, molecular hydrogen is the most promising eco-friendly, high-energy and economically viable alternative to fossil fuels [22, 24-34]. The energy yield of H2 combustion is 120 MJ/kg, which is much higher compared to carbon-containing fuel CH4 - 50 MJ/kg [23]. The final product of hydrogen combustion is water, which avoids the greenhouse effect [22, 24-39]. Hydrogen dark fermentation of organics is short-term and simply regulated process. It allows destroying of a wide range of hazardous organic waste quickly and effectively as well as obtaining of green energy biohydrogen [12, 40-42].
To develop effective industrial biotechnologies, it is necessary to investigate the efficiency and regularities of scaling of the fermentation process [7, 22, 43-46]. Thus, the goal of the present work is to review the process of scaling of multicomponent food waste destruction via its fermentation in anaerobic batch reactors while obtaining biohydrogen.
2. THE THEORETICAL BACKGROUND TO DEVELOP THE NOVEL HYDROGEN PRODUCING BIOTECHNOLOGY
The vast majority of modern environmental and bioenergy biotechnologies is empirical. In other words, a microbial community is selected with each type of waste (organic waste, metals, radionuclides). Then, the selected community performs the necessary reaction meaning the destruction of organic waste, metal reduction, synthesis of energy carriers, etc. Further, this technology is scaled and implemented in the industry. This approach has a significant methodological disadvantage. Such biotechnology might fail due to the slightest change in the concentration and the ratio of xenobiotics The vulnerability of biotechnology is predetermined by the lack of a theoretical background of the process that could provide its regulation, optimization and resumption in case of any negative changes. Therefore, we used the approach of thermodynamic prediction of the interaction of microorganisms with various classes of xenobiotics in any combination to develop novel universal environmental and bioenergetic biotechnologies.
First of all, we consider all xenobiotics (decaying organic waste, synthetic organic compounds, metals, radionuclides, etc.) as extreme factors in relation to microorganisms. This approach allows justifying the methodology for the creation of the conditions necessary for the existence of extremophilic microorganisms that can neutralize these extreme factors [47-51].
The stability of any organic and inorganic compounds is determined by Pourbaix diagrams in the coordinates of pH and Eh (redox potential, mV) [52, 53]. Knowing the “stability fields” of xenobiotics, it is easy enough to determine the conditions necessary for the destabilization of these compounds. The next step is to choose a chemical reaction that ensures the xenobiotic destabilization. The following step is a choice of the metabolic (biochemical) pathway carrying out this reaction. Finally, a physiological group of microorganisms that provides the necessary reaction is selected [54-56].
This approach can be explained by the example of the destruction of such a model food waste as potatoes. The starch is its main chemical component. Its destabilization (destruction) can be achieved due to oxidation by atmospheric oxygen. From the point of view of formal thermodynamics, starch can be oxidized by direct combustion or by oxidation of aerobic microorganisms [57]:
![]() |
(1) |
The alternative pathway to destabilize starch is by disproportionation [58]:
![]() |
(2) |
This reaction can be carried out both by high-temperature thermal cracking and microbial anaerobic digestion [58, 59].
The given examples illustrate the possibility of application of the thermodynamic prediction for the selection of alternative effective pathways for the destruction of organic xenobiotics, both physicochemically and microbiologically.
Consideration of non-biological pathways of destruction is beyond the scope of this article. Therefore, we will further consider in detail the sequence of stages of development of novel universal microbial technologies that can simultaneously achieve two strategically important goals. The first one is the quick and effective destruction of rotting natural polymers (vegetables, fruits, multicomponent food waste, etc.). The second is the production of molecular hydrogen as an environmentally friendly energy carrier.
For the processing (destruction) of solid rotting organic compounds, both aerobic (reaction 1) and anaerobic (reaction 2) types of microbial metabolism can be applied. Comparing them, it is obvious that microbial destruction under aerobic conditions is unacceptable for industrial implementation. Indeed, for the effective course of this reaction, it is necessary to observe the stoichiometric ratio of the components of the left side of the reaction equation, i.e. (C6H12O6)n and O2. Aerobic destruction is a heterophasic (three-phase) process. The first phase is solid polymer waste. The second phase is water, i.e. cultural medium. The third phase is molecular oxygen of the air. Obviously, none of the most effective aeration regimes can provide a stoichiometrically balanced transport of the oxidizing agent O2 to solid organic compounds as carbon and energy source. It is explained by the low solubility of O2 and the low rate of its diffusion from the gas phase to the aqueous. Hence, it is obvious that the rate of O2 diffusion into the culture medium will be much lower than the necessary amount for the destruction of concentrated organic compounds by aerobic microorganisms. Finally, during aerobic degradation of organic compounds no energy source as a final product is produced [60].
Therefore, it is necessary to search for an alternative metabolic pathway for the balanced destruction of organic compounds with the simultaneous production of energy carriers.
Anaerobic biochemical disproportionation of organic compounds, including starch, is carried out by both hydrogen and methanogenic fermentation. Since methane fermentation is a long and complex process, we will focus on the faster and more efficient hydrogen one [61, 62].
Under anaerobic conditions, microorganisms decompose polymers of both plant and animal origin with the synthesis of molecular hydrogen [62, 63]:
![]() |
(3) |
![]() |
(4) |
From the point of view of thermodynamics, hydrogen synthesis is based on the reduction of two protons to molecular hydrogen by electron donors formed during the oxidation of polymeric organic compounds. In fact, such reactions are disproportionation reactions in which one part of the molecule of the organic compound is oxidized and the other is reduced. So, during the destruction of glucose (starch monomer) carbon with the redox level of 0 is oxidized to carbon with the redox level of +4 (CO2). In this case, hydrogen with the redox level of +1 (H+) is reduced to hydrogen with the redox level of 0 (H2).
The thermodynamics and biochemistry of hydrogen fermentation of glucose are the most studied. Therefore, we will further examine in detail pathways to optimize the process of hydrogen fermentation of natural polymers using starch-containing waste on the example of potatoes.
In accordance with the Pourbaix equations the optimal conditions for the reversible reaction 2H+ + 2e = H2, are pH = 7.0 and Eh = -414 mV. Hence, it is necessary to create and maintain these strictly anaerobic conditions in the cultivation medium for the fast and efficient hydrolysis of starch of plant polymers to glucose and subsequent hydrogen synthesis.
To achieve anaerobic conditions in the laboratory and for industrial fermentation, displacement of dissolved oxygen by inert gases (Ar, N2, etc.) and the subsequent introduction of reducing agents (Na2S, Ti(III) citrate, etc.) are used. However, these methods are very expensive and technically complex. Therefore, to achieve anaerobic conditions, we use aerobic and facultative anaerobic microorganisms. Oxidizing an easily digestible substrate (soluble organic compounds), aerobic microorganisms quickly reduce molecular oxygen in the gas phase, as well as dissolved in the medium to water (Н2О). Under conditions of oxygen limitation, the redox potential of the culture medium decreases from +300...+400 mV to -150...-200 mV. As the result, optimal conditions are created for the growth of obligate anaerobic microorganisms, including hydrogen synthesizing. It should be noted that, simultaneously with hydrogen-synthesizing microorganisms, sulfate-reducing and methane-synthesizing bacteria also grow under anaerobic conditions. Obviously, sulfate-reducing bacteria compete with hydrogen-synthesizing ones. Moreover, H2S (the final metabolite of dissimilatory sulfate reduction) will inhibit the growth of hydrogen producers. So, sulfate anion (SO42-) must either be absent in the medium or should be in minimal amounts. If necessary, it can be precipitated with Calcium or Barium cations.
It is known that hydrogen-synthesizing microorganisms consume substrate and grow several times faster than methanogens. Therefore, in order to avoid the development of methanogens, it is necessary to ensure the fast and efficient growth of hydrogen-synthesizing microorganisms [43, 64]. To ensure such conditions, fragmentation (grinding) of polymer compounds (potatoes and other waste) is necessary. Indeed, the destruction of such polymers occurs on the surface of solid particles by the biofilm of microorganisms. It follows that the efficiency of hydrolysis is proportional to the total surface area of the particles, and fragmentation of the waste will certainly lead to an acceleration of the destruction (hydrolysis) of potatoes and increase in the efficiency of H2 synthesis.
However, the acceleration of the hydrolysis of starch on the surface of the particles leads to the inevitable accumulation of final metabolites (organic acids) in this zone and a strong local acidification of the medium. So, on the surface of the particles, the pH can decrease to 3.0-4.0, while for the thickness of the culture medium, its value is close to neutral [65]. To compensate such negative consequences, intensive mass transfer (mixing) of the waste is necessary to remove acidic metabolites from the surface of the particles. However, the removal of acidic metabolites leads only to their more uniform distribution in the culture medium. A further inevitable increase in their concentration over the entire volume of the medium will also lead to inhibition of hydrogen fermentation. Therefore, to eliminate the negative effects of acidic products, it is necessary to add pH buffers to neutralize the environment [38, 66, 67].
It is also necessary to take into account the weight ratio of solid waste and the aqueous phase (water added into the bioreactor). On the one hand, minimization of the volume of the liquid phase simplifies and cheapens the biotechnology. On the other hand, with small volumes of the liquid phase, the rapid accumulation of acidic metabolites in high concentrations will occur leading to the inhibition of the process. The neutralization of acidic metabolites partially reduces the toxic effect. However, neutral final products will inhibit fermentation by the feedback mechanism. Obviously, the determination of the optimal ratio of waste to liquid phase requires a separate study.
Thus, a detailed examination of the theoretical aspects of hydrogen fermentation of solid organic waste makes it obvious that this is a complex multi-level process. Its effectiveness is determined by a set of physical and chemical factors as well as fermentation indices. As the most important, we identified 11 of the following parameters: pH, redox potential, temperature, size of waste particles, mixing speed of culture medium, mixing frequency (ratio of duration of mixing and pause), ratio of solid (waste) and liquid (water) phases, design of a bioreactor, composition of microbial community, regulators of microbial metabolism, the concentration of dissolved organic compounds.
Currently, the average duration of the destruction of solid organic waste with the formation of hydrogen or methane in laboratory and industrial conditions is about 30 days. The indicated duration of fermentation is now considered quite acceptable for industrial biotechnology. However, we have shown that the control and regulation of these 11 parameters can increase the efficiency of hydrogen fermentation 10-20 times [43, 68]. So, experiments conducted in 2018 in the experimental-industrial anaerobic batch bioreactor with a volume of 240 L showed the possibility to complete the fermentation of multicomponent food waste in 3 days, and in 2019 - in 1.5 days.
In our opinion, the most important fermentation parameters, allowing to estimate the efficiency of the process and to scale the pilot-industrial technology to the level of large-tonnage industrial are the following: T (hours or days) - the duration of the fermentation; Kd - the coefficient of waste destruction meaning the ratio of the initial and final weight of waste, the yield of hydrogen (VН2, L) - the volume of hydrogen synthesized from 1 kg of waste counting to absolutely dry weight.
Important steps are the growth of microbial biomass, its preservation, transportation, and subsequent loading into the bioreactor. These steps are complex and expensive [69]. The slightest deviation from the procedure leads to the decrease in metabolic activity, or to contamination and even death of microorganisms. We completely solved this problem by using microbial pellets in the form of dry granular microbial preparation as the inoculum. Pellets contain viable microorganisms producing H2 in high concentration, the nutrients necessary for them and regulators of microbial metabolism. When pellets are added to an aqueous medium, a rapid and effective growth of microorganisms occurs, the synthesis of H2 begins after 12 hours. Thus, the fast and efficient fermentation of waste with the synthesis of H2 starts.
3. APPLICATION OF THE THEORETICAL APPROACH FOR THE EFFECTIVE SCALING OF HYDROGEN DARK FERMENTATION PROCESS
We have created a theoretical background and its practical application to develop effective biotechnology for dark hydrogen fermentation of multicomponent solid food waste more than 10 years. During this time, on the basis of thermodynamic prediction, a theoretical model of the process of fermentation of organic compounds was created. It became the basis for the subsequent scaling of the process, studying of its dynamics and optimizing the key parameters of fermentation.
The successful scaling of the process is the indicator of the high efficiency of our approach. The high fermentation efficiency was evidenced by the obtained fermentation parameters: the duration of the process T (hours or days); the coefficient of waste destruction Kd; hydrogen yield VН2 (L).
The scaling of the waste fermentation process took place in three stages:
(1) Laboratory - study of the dynamics and optimization of waste fermentation in laboratory flasks with the volume of 0.5 L;
(2) Laboratory - study of the dynamics and optimization of waste fermentation in a laboratory bioreactor with the volume of 20 L;
(3) Experimental-industrial - the study of the dynamics and optimization of waste fermentation in an experimental-industrial fermenter with the volume of 240 L.
At the first stage, the optimization of waste fermentation was carried out using laboratory flasks with the volume of 0.5 L (Fig. 1). Potato (45 g) was used as a model substrate to which 0.25 L of sterile tap water as well as microbial pellets were added.
As the result of a series of experiments in laboratory conditions in flasks, preliminary results of waste fermentation optimization were obtained. The necessity to maintain pH values within 6.0...7.0, and the redox potential in the range -400...-200 mV was shown. These values were defined as optimal for microbial growth and hydrogen synthesis. Under such conditions, hydrogen synthesis appeared to start on the first day of fermentation. The maximum hydrogen concentration (35%) was reached after 28 hours. Maintenance of the optimal pH was achieved by the periodical addition of the regulators of microbial metabolism to neutralize the toxic effects of microbial exometabolites.
Thus, the following fermentation parameters were determined. The duration of the process (T) was 3.4 days. The coefficient of waste destruction (Kd), i.e. the ratio of the initial and final weight of waste reached 84, and hydrogen yield (VH2) was 43 L/kg of waste counting on the absolutely dry weight.
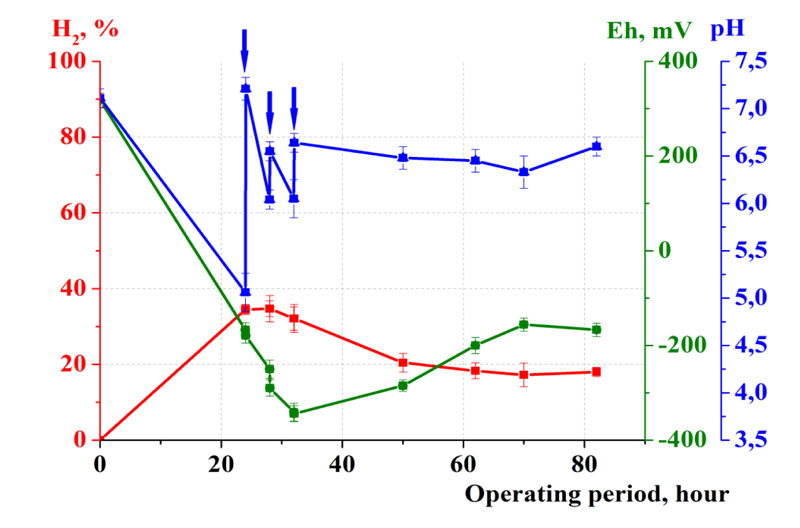
The experiments showed the fermentation of multicomponent food waste to be promising to obtain high-calorie energy carrier H2.
Thus, to develop effective industrial biotechnology, the next step was the study of dynamics and optimization of fermentation in the laboratory bioreactor with the volume of 20 L (Fig. 2).
For this purpose, pasteurized waste containing potatoes, tomatoes, cucumbers and chicken fillet in equal ratios (2 kg) and 6 L of tap water were loaded into the bioreactor. Also, microbial pellets and regulators of microbial metabolism were added to the bioreactor. The reactor was hermetically sealed with rubber stoppers with fittings to load the regulators of microbial metabolism, to sample the culture fluid and to discharge the synthesized gas into the gas holder.
As the result of the studies, the effective maintenance of optimal pH and redox potential of the culture medium was shown to be achieved by optimization of the regulation and mixing mode of the waste in the bioreactor, as well as the ratio of the weight of waste and water. So, the following optimized parameters were used: the ratio of the weight of solid and liquid phases 1:3, the speed of the rotor of the mixer 24 rpm, and the mass transfer mode 5 min of mixing and 60 min of pause. The maximum hydrogen yield was VH2 = 120 L/kg of waste achieving at the maximum concentration of H2 in the gas phase 44% (Fig. 3).
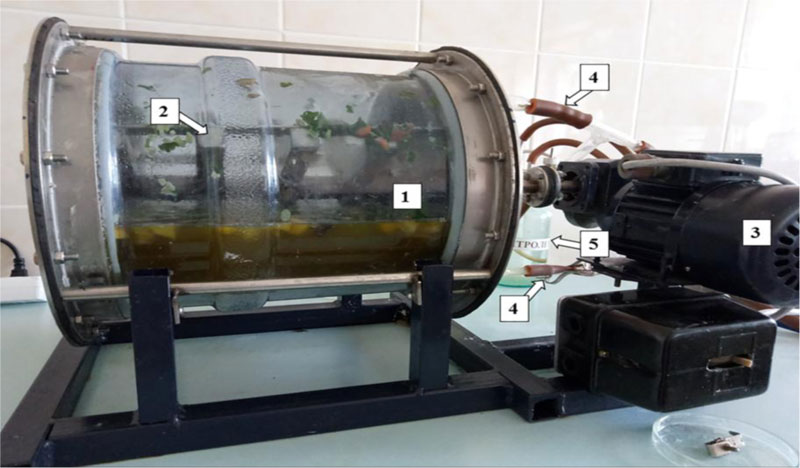
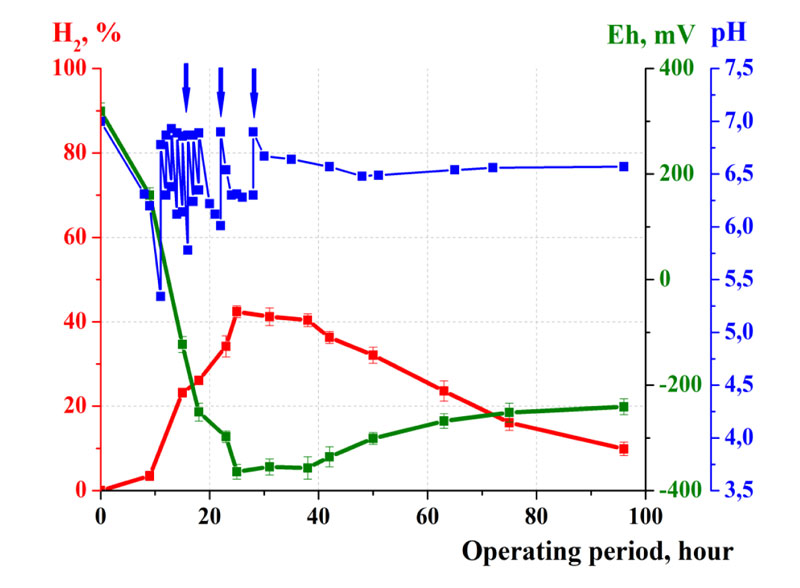
It was found that such fermentation mode provided a high rate and efficiency of waste destruction. So, the fermentation time (T) was only 3 days, and the coefficient of waste destruction Kd = 90. Such a high fermentation efficiency was achieved as the result of the process optimization. Thus, applying the ratio of solid and liquid phases 1:3, the concentration of organic compounds was high for rapid fermentation and hydrogen synthesis, however, microorganisms were not inhibited by the excessive accumulation of toxic exometabolites. At the same time, the amount of water used was minimized, allowing us to save resources and use bioreactors of minimal volumes. In addition, the optimized fermentation mode provided mixing of the culture mixture ensuring the effective interaction of microorganisms, waste particles, and microbial metabolism regulators. Under such conditions, a uniform distribution of all components was achieved. It resulted in the maintenance of the pH and redox potential of the culture fluid at the optimal level. Therefore, active microbial growth and hydrogen synthesis took place.
Thus, high efficiency of 40-fold scaling of fermentation from the bioreactor with the volume of 0.5 L to the laboratory bioreactor with the volume of 20 L was achieved. Optimization was shown to provide high effectiveness of waste destruction and hydrogen synthesis.
The scaling of the process with the application of experimental-industrial anaerobic batch bioreactor with the volume of 240 L was the following stage of the investigation (Fig. 4).
The investigation of the dynamics of hydrogen fermentation and optimization of experimental-industrial process was carried out in this bioreactor. In 2018, the destruction of the following mixture of waste took place: potatoes (7.5 kg), apples (4.5 kg), pasta (2.0 kg), bread (1.5 kg), rice with vegetables (0.5 kg), dumplings with cabbage (0.5 kg), buckwheat porridge (1.0 kg), muesli (0.5 kg), slices of peas (0.5 kg), bananas (0.5 kg). The ratio of waste and water was 1:8.
In 2019, the content of waste was the following: potatoes (27 kg), cucumbers (0.45 kg), zucchini (0.45 kg), tomatoes (0.45 kg), carrots (0.45 kg), chicken fillet (3.5 kg). The ratio of waste and water was 1:4.
The following mode of mass transfer was applied: 5 min of mixing / 60 min of pause.
The design of the bioreactor provided the effective mass transfer of the fermentation mixture as well as destruction of organics and synthesis of biohydrogen.
The investigations revealed the possibility of effective scaling of fermentation of organics in the experimental- industrial batch bioreactor. Obtained results showed similar fermentation parameters for both small laboratory and large experimental-industrial bioreactors.
The efficiency of fermentation in large scaled bioreactor was also high. Time detention (T) was 4 days (Fig. 5). During the initial 12 hours of fermentation, the pH of the culture medium decreased from 6.0 to its minimum value of 3.9. The maintenance of optimal pH values (pH = 6.0…7.0) was provided by the addition of regulators of microbial metabolism. The acceptable pH = 6.3 was achieved after 14 hours of fermentation. Under such conditions, the pH value changed gradually, so the need for regulation was only during the first day of cultivation (Fig. 5).
Optimal pH values allowed reaching and maintaining optimal Eh value. The redox potential decreased to -320 mV after 14 hours of cultivation. Throughout the technological cycle the Eh remained within the values optimal for hydrogen fermentation of waste (-250...-380 mV). Active hydrogen synthesis occurred at low values of Eh = -300...-380 mV during 40 hours (since 20 till 60 hours) (Fig. 5).
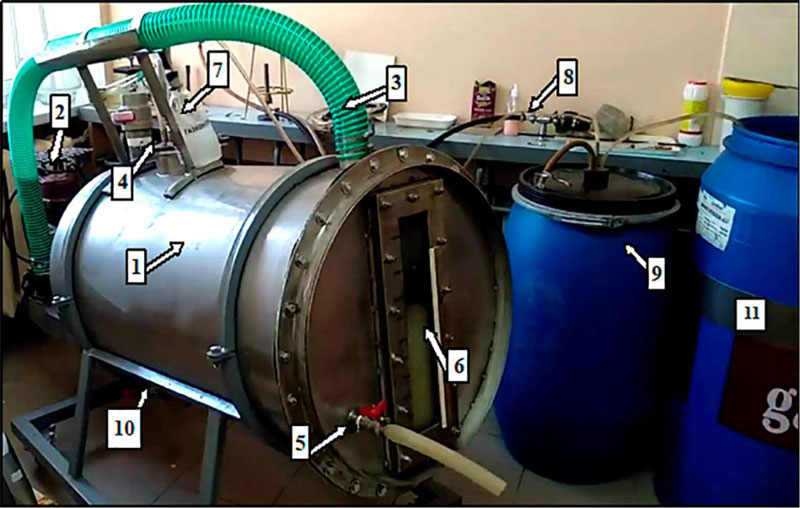

High efficiency of digestion of multicomponent food waste in the large scaled experimental-industrial bioreactor was confirmed by the following fermentation parameters. Time detention (T) was 4 days. The coefficient of waste destruction (Kd) was 140. The molecular hydrogen yield (VH2) was 90 L/kg of dry waste counting. The maximum concentration of H2 was 50%.
Continuation of the investigation and optimization provided a significant decrease in the duration of fermentation (Т) to 1.5 days (Fig. 6).
Optimization of the ratio of weight of waste and water (1:4) led to an increase in the concentration of hydrogen in the gas phase up to 58%. The redox potential of culture medium decreased after 9 hours of fermentation from +300 mV to -300 mV, and remained within -350…-300 mV during the fermentation. Due to effective regulation, the values of рН were maintained in the optimal range 6.3…6.7. Under such conditions, high effectiveness of waste destruction was achived: Kd = 86. Hydrogen yield was VH2 = 45 L/kg of waste.
Along with the obtaining of green energy carrier, molecular hydrogen non-digested lignocellulosic residues after fermentation is another valuable product (Fig. 7). It can be dried in the open air and used as high-energy fuel [43]. Moreover, obtained data showed the possibility of using lignocellulosic residues as the biofertilizer in depleted soils [70].
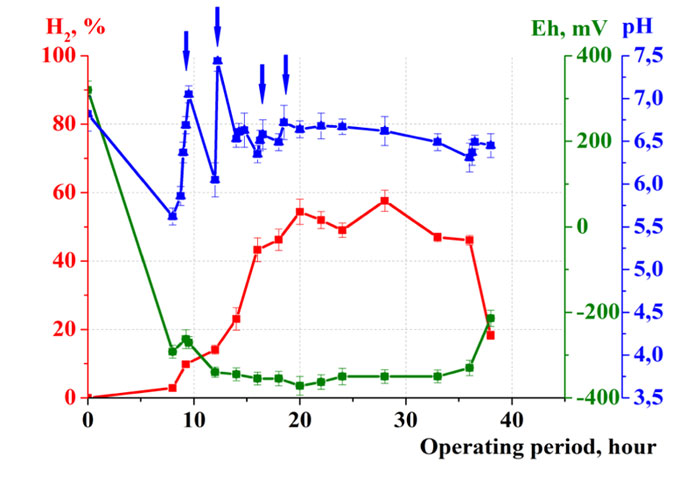
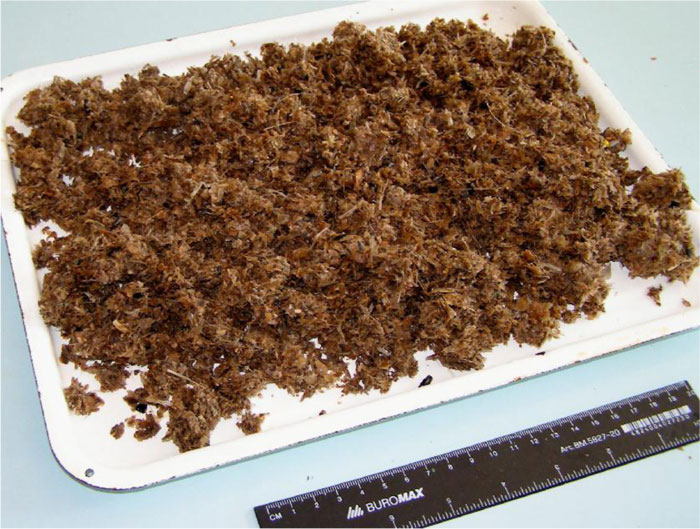
Thus, obtained results showed the high efficiency of the destruction of multicomponent food waste and biohydrogen synthesis during the scaling of the process to the stage of the experimental-industrial bioreactor. Its design provided the effective mass transfer of culture medium and maintenance of optimal fermentation parameters.
4. THE PROSPECTS OF THE INDUSTRIAL IMPLEMENTATION OF THE BIOTECHNOLOGY
Hydrogen dark fermentation is a promising process to destroy effectively hazardous multicomponent food waste with simultaneous production of green energy molecular hydrogen. Our investigations showed high efficiency of the fermentation in laboratory conditions as well as in the experimental industrial ones [12, 43, 68].
Obtaining biohydrogen via dark fermentation is a promising process for the generation of green energy at the industrial level. It involves a number of microbial processes for the degradation of hazardous organics with synthesis green energy biohydrogen [9, 71-74]. The first attempts of our investigations of hydrogen dark fermentation of organics were started about 10 years ago [75, 76]. Initial general regularities of the process were obtained in laboratory flasks. Then simultaneous dynamics of fermentation parameters were confirmed in small laboratory scaled bioreactor with the volume of 20 L [43]. Further scalling of the developed biotechnology was the next necessary step to confirm its efficiency and possibility of industrial implementation. So, that was the reason to develop the design of the experimental-industrial batch bioreactor with the volume of 240 L and continue the investigation of fermentation process.
Literature data indicate the necessity to maintain optimal partial pressure of H2, the concentration of additional macro- and micronutrients, the design of a bioreactor, the content of inoculum and substrate [22, 44]. We found that the efficiency of food waste destruction and molecular hydrogen synthesis also depended on the following fermentation parameters: temperature, pH and Eh of culture medium, the ratio of the solid phase (solid particles of waste) and liquid (water), the size of waste particles, the frequency and speed of waste mixing, etc. Our laboratory investigations led to their optimization increasing the efficiency of hydrogen dark fermentation of food waste [43, 68]. Obtained techniques of fermentation were successfully applied in the experimental-industrial batch bioreactor.
The approach we used is based on the thermodynamic calculations of microbial metabolism and interaction with xenobiotics [12]. Fermentation of organics with H2 synthesis was shown to be an effective process [34, 77-79]:
Starch → Hydrolysis → C6H12O6 + 2H2O = 2CH3COOH + 2CO2 + 4H2, ∆Go = -184 kJ/M.
It requires minor technical operations to control and regulate the process. Most of them are intended for the regulation of microbial metabolism to avoid inhibition of microbial growth [12, 80].
During the fermentation of organics, microorganisms excrete metabolites (dominantly fatty acids and alcohol). Accumulating in the culture fluid, they become toxic to microorganisms. In this regard, microbial growth is inhibited resulting in the decrease in the efficiency of hydrogen synthesis and waste destruction [22, 43, 66, 68, 81-83].
The decrease in the concentration of waste in the culture fluid during their fermentation was shown to contribute to the increase in the efficiency of waste destruction and hydrogen synthesis. To avoid the inhibition of microbial growth due to high concentration of exometabolites it is reasonable to maintain optimal concentration of initial substrate. On the one hand, to reduce the costs, it is necessary to use the smallest amount of additional water in the bioreactor. The volume of water should be sufficient to avoid too high concentration of organics in solution. Earlier optimized ratio of solid and liquid phases was shown on the laboratory bioreactor [68]. Similar approach was used to study the effectiveness of molecular hydrogen synthesis and waste destruction in the experimental-industrial bioreactor. The fermentation was carried out using the ratio of solid phase (food waste) to liquid (water) 1:8 and 1:4. Such concentration of waste would not lead to a high concentration of toxic exometabolites in the culture fluid. Therefore, the growth of microorganisms will be maintained at an optimal level. The mass transfer of culture mixture in the bioreactor is another important fermentation parameter. Optimal mass transfer provides effective interaction of microorganisms with solid food waste and regulators of microbial metabolism. Moreover, it ensures the washing of toxic microbial exometabolites from the surface of solid waste particles to increase the effectiveness of fermentation [43, 68].
High efficiency of fermentation can be reached due to the effective design of the bioreactor. Now different types of bioreactors are used for digestion organics [84-87]. Most of the dark fermentative hydrogen production studies are carried out in a batch Continuous Stirred-Tank Reactor (CSTR) under wet conditions (<10% total solids). Besides CSTR, many studies have been carried out in Anaerobic Fluidized Bed Reactor (AFBR), Anaerobic Sequencing Batch Reactors (ASBR), fixed or packed bed reactors, Upflow Anaerobic Sludge Blanket Reactors (UASB), leaching bed reactors, anaerobic baffled reactors, plug flow reactors or Membrane Bioreactors (MBR) and with an objective to enhance the biohydrogen yield and production rate [22, 88-90].
The design of the bioreactor is important to provide effective destruction of waste and hydrogen synthesis. The construction of the designed bioreactor ensures even mixing of waste, regulators of microbial metabolism, and microorganisms providing their effective interaction. Also, horizontal arrangement of working chamber provides increase in the efficiency of gas extraction, including hydrogen. As the scale increases, the surface area of the culture fluid / air phases increases, improving the fermentation process. Such bioreactor provides effective fermentation of a wide range of organic waste (both domestic and industrial food waste, and agricultural organic waste) with the obtaining of H2.
The design of the bioreactor was developed to have the possibility of scaling. Such installation can be applied for both domestic and industrial waste volumes. The development of such a biotechnological reactor is promising for its further direct implementation in small farms as well as in large enterprises.
In addition, optimal volume of liquid phase (the ratio of waste to the liquid phase is 1:4) prevents the accumulation of a wide range of toxic for microorganisms exometabolites. As a result, their growth is not suppressed and the efficiency of digestion of waste with the synthesis of hydrogen increases.
So, the developed biotechnology based on the experimental-industrial batch bioreactor will solve a range of problems:
- To stop the inhibition of microorganisms and the process of fermentation as the result of the rapid accumulation of exometabolites at high concentrations;
- To provide an intensive mass transfer of culture medium to increase the efficiency of degradation of multicomponent organic waste and synthesis of molecular hydrogen;
- To facilitate the regulation of microbial metabolism in order to provide optimal conditions for the growth of microorganisms;
- To provide the possibility of scaling the developed bioreactor for the processing of industrial volumes of multicomponent organic waste;
- To achieve maximum efficiency of the process of biohydrogen synthesis and waste destruction.
The technology of multicomponent food waste fermentation has an excellent potential for industrial hydrogen production. Its implementation can simultaneously solve two global problems: to reduce the weight and volume of environmentally hazardous waste, and to obtain environmentally friendly high calory energy carrier H2. However, now hydrogen fermentation can not reach the theoretically calculated level of 4 M (89.6 L) H2 output per 1 M (180 g) of glucose, since the maximum yield reached 33% [22, 83, 91].
Wu et al. [92] reported that they obtained 147.1-202.7 L H2 per 1 kg of glucose in fermentation of pork manure with glucose addition. Xing et al. [93] obtained an enhanced yield of H2 31.5 L/kg volatile solids of milk fertilizers. Ren et al. [94] demonstrated that the digestion of waste molasses yielded 585.3 L H2 from 1 kg of substrate [22]. Though there are many investigations of hydrogen production via fermentation of organics, the process still needs to be improved.
Effective destruction of food waste with simultaneous obtaining of environmentally friendly energy carrier (hydrogen) is of interest for both fundamental research and industry. However, modern biotechnologies for the recycling of food waste have serious disadvantages. The first one is the low hydrogen yield [95, 96], and the second is the low efficiency of waste destruction. Wang showed obtaining only 65 L of H2 per 1 kg of organic waste via its fermentation [95]. In addition, in order to increase the efficiency of hydrogen synthesis, economically disadvantageous thermophilic modes of fermentation of multicomponent organic waste are often used. In this case, the yield of hydrogen increases slightly from 63 (mesophilic regime) to 81 L/kg of waste [96].
At the same time, combining the design of the experimental-industrial bioreactor with the regulation of microbial metabolism, we provided higher yield of hydrogen up to 90 L/kg of waste. It should be emphasized that there are data in the available literature on the efficient hydrogen fermentation of certain types of substrates [73, 97]. Of course, large volumes of hydrogen 150 L/kg and 311 L/kg of waste [73], respectively, were obtained during the fermentation of wastes of corn starch - macromolecular plant polysaccharide [97] and monosaccharide-hexose. We have created the representative mixture of food waste as close as possible to environmentally hazardous household and industrial food waste. The waste used in our experiment also consisted of potato-starch raw materials of 40%. However, potatoes contain no more than 8-15% of starch [98]. Based on this, our waste contained about 6% of starch. According to theoretical calculations, the rest of the used vegetables contained no more than 4% of starch. Thus, the multicomponent organic waste used in our experiment contained no more than 10% of carbohydrates. This index is 10 times smaller than during fermentation of pure hexose and pure corn starch [73, 97]. Current studies also indicate a low efficiency of food waste degradation, which fluctuates within 40-80% [97, 99], corresponding to Kd = 2.5-5.0. In our work, a highly efficient waste degradation rate was obtained - 99% (Kd = 140), which is 28 times higher [97].
Moreover, it should be emphasized that conventional duration of fermentation process takes plase during continuous time (up to 1 month). That is why microbial technologies of hydrogen obtaining are not implemented in the industry. Additionally, obtaining hydrogen from MCFW is a complicated task [18, 100, 101]. The optimized biotechnology and regulation of fermentation parameters contributed to the reduction of the time detention to 1.5-4 days. This is due to the effective optimization of the fermentation mode, as well as the regulation of microbial metabolism. It provides conditions necessary for the consistent growth of specific physiological groups of microorganisms.
It is known that the dominant microbial group of the fermentation mixture consists of bacteria of Bacillus and Clostridium genera. Acting together, these groups of aerobic (Bacillus) and anaerobic (Clostridium) microorganisms enhance the metabolic activity of each other, providing high efficiency of waste destruction with H2 synthesis. The distinctive positive feature of aerobic bacterial group (dominantly Bacillus spp.) is high resistance to extreme factors (long storage, desiccation, toxic metals, etc.), high growth rate and metabolic activity. Their growth starts during the fermentation of MCFW. Hydrolising organic polymers of waste consume oxygen dissolved in the solution and present in the gas phase of the bioreactor as well as lower the redox potential of solution to -200…-100 mV providing the optimal conditions for growth of anaerobic microorganisms. The physiological group of anaerobic microorganisms consists presumably of Clostridium genus. They also possess high resistance to extreme factors and high metabolic activity. They start growing at the redox potential to -200…-100 mV decreasing it to -400…-300 mV. Such conditions are optimal for hydrogen synthesis they carry out with high efficiency [22, 44, 83, 102].
The key factors influencing the yield of hydrogen are the regulation of pH and Eh, as well as periodic mixing of solid food waste providing conditions necessary for active growth of microorganisms and effective fermentation [43, 103-105]. Obtained results confirmed the assumption that the optimization of the design of the bioreactor will lead to a significant increase in the efficiency of biotechnology. The design of the bioreactor, regulation of pH and redox potential, as well as mass transfer, were key factors in increasing the synthesis of hydrogen, the efficiency of waste destruction and shortening the duration of fermentation.
Thus, the application of experimental industrial bioreactor is industrially promising as it provides high efficiency of hydrogen fermentation of waste and facilitates the process of regulation of microbial metabolism. Сonducted research showed the possibility of successful scaling of developed biotechnology. It revealed its potential for further direct application in small farms, large enterprises, etc.
CONCLUSION
The developed biotechnology was shown to be effectively scaled up to the experimental-industrial batch bioreactor to provide a fast and efficient digestion of multicomponent solid food waste along with the simultaneous production of biohydrogen. Horizontal stereometry of the reactor and a powerful pump outside of the working chamber to provide the mass transfer are distinctive positive features of the industrial batch bioreactor designed.
CONSENT FOR PUBLICATION
Not applicable.
FUNDING
The study was financially supported by the Comprehensive Program of Basic Research of the NAS of Ukraine “Fundamental problems of hydrogen and renewable energy and fuel cell technologies”: Grant # 2-18 «Development of optimal mode to maintain stable physical and chemical conditions (pH and ORP) for efficient degradation of multicomponent food wastes with the production of biohydrogen in the horizontal reactor», Grant # 2-18 «Development of the construction of universal installation for obtaining of biohydrogen from multi component organic waste», as well as by the Target Research Program of the NAS of Ukraine “Development of scientific bases for hydrogen production, storage and application in autonomous energy supply systems” for 2019-2021: Grant # 1-19 «Increase in the yield of biohydrogen in the experimental-industrial installation with a volume of 240 liters due to optimization of fermentation parameters of pH, redox potential, mass transfer mode, etc.»
CONFLICT OF INTEREST
The author declares no conflict of interest, financial or otherwise.
ACKNOWLEDGEMENTS
Declared none.