All published articles of this journal are available on ScienceDirect.
Plant Feedstocks and their Biogas Production Potentials
Abstract
Introduction:
Nowadays, organic waste utilization and replacement of fossil energy sources with their renewable alternatives pose a challenging problem both for industrially developed and developing countries. Anaerobic digestion of organic biomass into biogas is considered an efficient technology for bioenergy production. Over the period from 2009 to 2018, the global biogas production capacities have more than doubled and are continuing to grow. The composition and the amount of biogas depend strongly on the type of the substrate. Various types of feedstock can be used for the production of biogas such as animal wastes, agricultural residues, and dedicated energy crops.
Objective:
To review biogas production potentials of energy crops and plant processing raw materials.
Results:
In the background of historical development and present state, the paper reviews the potential of different plant raw materials to be utilized for biogas production purposes. The potential of energy crops, agricultural residues, and wastes for biogas production is analyzed. International projects concerning energy crops grown on marginal lands are presented and commented on in the article. The approach of implementing crop rotation systems for industrial energy crop cultivation is described and recommended as beneficial for various purposes. The anaerobic degradability of biomass constituents, optimal process parameters, and biomass treatment for biogas production are discussed. C/N ration and lignocelluloses content in the substrate are considered among the most decisive parameters for AD and methane production. Various concepts of biogas bioreactor technologies have been studied depending on the substrate type.
Conclusion:
Plant feedstock may play a decisive role in biogas production as a renewable energy source. To avoid GHG release into the atmosphere, biogas facilities should be built within the closest vicinities to the places of existing garbage dumps, and waste management practice involving organic fraction separation in households and in the industry should be applied. Construction of biogas facilities is beneficial for environmental, economic, and social reasons.
1. INTRODUCTION
The human population on the Earth is steadily growing which leads to the increase in food and energy demands and aggravates the environmental challenges. Replacing fossil fuels with renewable energy alternatives has become a major global issue of the XXI century and a key to sustainable development [1]. Biogas is a form of renewable fuel and an energy source, it is a combustible gas mixture produced during anaerobic fermentation of biomass by bacteria [2]. Successful implementation of biogas technologies transforms costly, environmentally damaging and socially sensitive issues of fossil fuel dependence, environmental pollution, Greenhouse Gas (GHG) emissions and waste utilization into a profitable solution producing electricity, heat and biofertilizers. The biogas technology can also produce a vehicle fuel and substitute fossil gas when upgraded to methane [3, 4]. Development of a national biogas production sector can significantly contribute to the establishment of new enterprises, bring more income to rural areas, create new jobs and improve living standards [5].
Methane fermentation is well known to occur in nature, for instance, in the process of organic matter decay in an oxygen-deprived environment such as landfill wastes and swamps [1, 4, 6]. Raw biogas consists mainly of 50–75% methane (CH4), 25-50% carbon dioxide (CO2); the rest is composed of water vapor (H2O) and traces of oxygen (O2), nitrogen (N2), and hydrogen sulfide (H2S) [7]. Biogas containing 55% CH4 has a calorific value of 21.5 MJ/Nm3, while pure CH4 has a calorific value of 35.8 MJ/Nm3, therefore this is the reason to remove CO2 from raw biogas [2]. To prevent methane release into the atmosphere, the biogas collecting facilities should be located in the closest possible vicinity to the existing garbage dumps. Waste management involving organic fraction separation in households and in the industry should be applied [8, 9].
From the historical perspective, ancient Persians observed that rotting vegetables release flammable gas [10]. Marco Polo reported that sealed sewage tanks, made for biogas collection two-three thousand years ago, were mentioned in ancient Chinese literature [10, 11]. The development of anaerobic digestion (AD) technology was pioneered in 1859 in Bombay as a wastewater treatment installation [10]. Using the septic tank, that had been invented by Mouras and improved by Cameron, the government of Exeter in England endorsed in 1897 the treatment of the entire city’s wastewater for heating and lighting purposes [6]. In the 1930s, the initial ideas were further developed in the USA to utilize cellulose-rich waste for biogas production. At that time, methane production from farm manure was implemented in India, and wealthy families built some rural biogas plants in China [11]. The first agricultural biogas plants in European colonies were constructed in Algeria, and after World War II that experience was implemented in southern France and Italy [11]. The application of AD systems was stimulated in the early 1970s by a steep rise in fossil fuel prices and by the increasingly stringent pollution control regulations [6]. Nowadays, the AD technology that allows the generation of renewable energy while treating biodegradable waste and mitigating GHG emissions is becoming an even more topical and important issue [12].
According to the International Renewable Energy Agency [13], from 2009 to 2018, the biogas production has more than doubled in the world, starting from 8 280 MW in net electricity generating capacities and increasing to 18 126 MW. The European countries account for 70-74% of the world biogas capacities with the leading country Germany (50-53% from the total European biogas capacities, 6 583 MW in 2018). The USA is the second-largest biogas manufacturer in the world after Germany producing 2 384 MW in 2018 but driving up not as fast as Germany. Italy is the second country in Europe and the third in the world with 1 432 MW of biogas capacity in 2018; it increased biogas net generating capacity four times compared to the level in 2009. The Asian countries have built lots of micro biogas plants, and the leaders in the number of country biogas plants in the world are China, India, and Nepal with 12 mln, 3.7 mln, and 140 thousand biogas operating facilities, respectively [14].
The biogas potential and its composition are largely determined by the source [1]. Biogas is a product of biomass (a biological material available on a renewable basis) fermentation that generally includes organic wastes, plant residues and dedicated energy crops (DEC) [15]. The organic wastes suitable for biogas production include animal waste such as dairy manure and poultry litter, municipal solid waste, wastewaters and sludge, industrial waste, such as food processing waste, is also suitable for the purpose. Biogas production from waste materials is consistent with a closed-loop circular economy concept which aims at reducing both virgin material inputs and waste outputs [8] and the “Waste-to-Energy” trend [1].
Agricultural (or crop) residues are the non-edible portion of plants that remain on the fields following harvesting and which are distinguished from other biomass resources (e.g., DEC) as they are not in most cases produced specifically for energy purposes [15]. Reuse of plant residues is a cheap source of biomass and is more benign since landfill sites will inevitably generate methane and other gaseous emissions that increase the environmental burden [16].
Energy crops are specifically cultivated for fuel and are therefore designed to maximize energy yields per hectare at the lowest possible costs [16]. At present, biogas production is becoming more controversial where arable land is taken up with large scale cultivation of energy crops or where feedstock has to be transported over a long distance to reach a production facility [17]. At the same time, obtaining biogas from DEC can also be beneficial, particularly where a limited proportion of energy crops can be supplemented with organic waste and thus enhance the production process [17]. Besides, the cultivation of industrial DEC on marginal, degraded or abandoned land can be considered as a compromise way to minimize land-use competition with food crops [18-20].
Although the AD process is a widely implemented technology with several thousand full-scale plants in operation, there are still significant research gaps concerning process control and integration, process stability, microbiome and environmental analyses [12]. To realize the potential of the AD technology for energy, biochemical production and environmental protection, a comprehensive analysis needs to be conducted with various available feedstocks [12]. The objective of the current article is to review biogas production concerning energy crops and plant processing raw materials.
2. PLANT FEEDSTOCKS
In European countries, up to 70% of the feedstock used for biogas production comes from the agricultural sector such as DEC, manure and agricultural residues [21]. According to the European Biogas Association (Fig. 1), DEC constitute 50 or more percent as a substrate for biogas production in Austria, Cyprus, Germany, and Latvia; for comparison, agricultural residues account for 40-60% in biogas generation in Cyprus, Germany, Denmark, France, Italy and Poland among the 16 countries analysed.
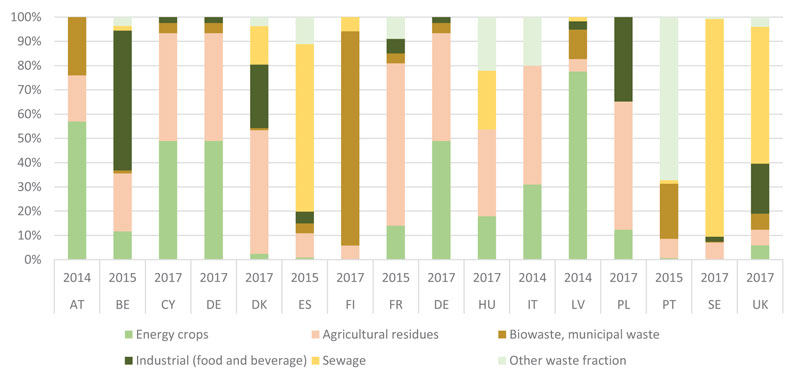
The Green Gas Grids project, which ran from 2012 to 2014, was funded by the Intelligent Energy Europe programme, forecast a maximum technical biogas production in the EU-28 in the range of 150 to 250 billion cubic meters (Bcm) per year in natural gas equivalent terms, comprising around 100 Bcm from residues, and 50-150 Bcm/year from energy crops [17].
2.1. Energy Crops
Energy crops can be herbaceous as grass, maize (Zea mays L.), raps (Brássica nápus L.) or woody like willow (Salix), poplar (Populus), oak (Quercus), although the woody crops need special delignification pretreatment before AD [5]. The high content of lignin is not degradable in AD and makes the woody substrates more suitable for gasification or incineration or for the composting process as a bulking agent instead of biogas production [22]. Herbaceous energy crops have several essential characteristics that make them suitable for AD: efficient solar energy conversion resulting in high yields, low agrochemical inputs, low nutrient and water requirement due to their extensive rooting system, which holds onto fertilizers and water, and low moisture levels at harvest [15]. Plants with perennial growth habits also have the benefits of low establishment costs and fewer annual operations [15]. Using crops producing large biomass yields and/or growing fast crops that can provide high biogas output as a feedstock source makes biogas production cost-effective and profitable [23].
Key determining factors for a maximum biogas yield are the following: species and variety of energy crops, time of harvesting, mode of conservation and pretreatment of the biomass prior to the digestion process and nutrient composition [24]. Clearly, DEC which are more suitable for cultivation in one country might be less suitable for the other country [25]. To enhance the biogas production process from agricultural residues, manure and organic waste, energy crops such as maize, triticale (× Triticosecale) and sweet sorghum (Sorghum bicolor L. Moench) are often used [26].
To date, maize is the dominant substrate among energy crops for biogas production [25, 27-32] because it is assumed to possess the combination of high biomass (9-30 tons dry matter (DM) per hectare) and methane yields [24, 28, 29, 33-35]. Meanwhile, methane yield depends not only on the kind of crop and the genotype but also on biomass treatment [32, 36]. Some research investigations, presented in Table 1, found no differences in methane content between maize and barley (Hordeum vulgare L.), rye (Secale cereale L.), triticale [32] and several other energy crops [29, 31, 32, 34].
Maize (whole crop) | 205 – 450 | Barley | 353 – 658 |
Wheat (grain) | 384 – 426 | Triticale | 337 – 555 |
Oats (grain) | 250 – 295 | Sorghum | 207 – 387 |
Rye (grain) | 283 – 492 | Peas | 390 |
Grass | 298 – 467 | Alfalfa | 340 – 500 |
Clover grass | 290 – 390 | Sudan grass | 213 – 303 |
Red clover | 300 – 350 | Reed Canary Grass | 340 – 430 |
Clover | 345 – 350 | Ryegrass | 390 – 410 |
Hemp | 355 – 409 | Nettle | 120 – 420 |
Flax | 212 | Miscanthus | 179 – 218 |
Sunflower | 154 – 400 | Rhubarb | 320 – 490 |
Oilseed rape | 240 – 340 | Turnip | 314 |
Jerusalem artichoke | 300 – 370 | Kale | 240 – 334 |
Potatoes | 276 – 400 | Chaff | 270 – 316 |
Sugar beet | 236 – 381 | Straw | 242 – 324 |
Fodder beet | 420 – 500 | Leaves | 417 – 453 |
Maize is considered to be one of the three major cereal-based calorie sources for food supply, along with wheat and rice [37], which brings controversy over the concurrent use of the crop for food or fuel. It is important to note that maize monocultures may facilitate soil erosion [38], nitrate leaching [39], cause negative long-term effects on soil organic matter and reduction of biodiversity [28]. Maize is also sensitive to water deficit and other environmental stresses abound flowering [40]. In Germany, maize-specific pests Diabrotica virgifera subsp. virgifera has become increasingly important [41] and encourages investigations of other energy crops for biogas production [28].
Concerning DEC, recent EU projects, such as presented in Table 2, and extensive scientific evidence suggest that ‘second-generation’ lignocellulosic feedstock production systems (e.g., switchgrass (Panicum virgatum L.), miscanthus (Miscanthus × giganteus J.M.Greef & Deuter), cardoon (Cynara cardunculus L. var. altilis), giant reed (Arundo donax L.), and removal of crop residues) are amongst the most promising candidates to be grown on less favourable agricultural lands [23, 42-45]. For example, it was shown [23] that the use of alternative energy crop A. donax comparing to maize silage decreased climate change impact because of high biomass productivity per specific area and inputs, low agronomic inputs necessary (operation, fuel, chemicals) to produce the biomass and reduced need of N and P allowing better nutrient management.
In the framework of the MAGIC project Table 2, the concept of marginal agricultural land low-input systems for industrial crop cultivation was introduced [46] as sets of agricultural low-input practices to form viable cropping systems on marginal agricultural lands under specific climatic conditions. Additionally, Horizon2020 project BIOPLAT-EU aims at promoting and supporting the uptake of sustainable bioenergy projects on marginal, underutilized and contaminated lands, and for this purpose, the project is producing a tool and a database of maps through a web-based platform [47].
Ukraine is a large country in Central and Eastern Europe with a territory of 60.4 mln ha 70% of which is agricultural lands [48]. As estimated in the international project FORBIO Table 2, 4 mln ha in Ukraine have been set-aside and can be used for DEC cultivation [49]. As long as the war in the Eastern part of Ukraine is making a badly detrimental impact on land and water resources, the study supported by NATO Science for Peace and Security Program [50] shows a good potential of Miscanthus x giganteus phytomanagement on metal (loid)-polluted military soils in Ukraine and Slovakia. Furthermore, the data [51] indicates that Miscanthus × giganteus could improve the composition and structure of marginal lands as it leads to an increase in soil organic content, reduces the bulk density, improves the microbial activity and soil porosity. Several EU projects such as MISCOMAR and MisChar also focus on Miscanthus biomass options for contaminated and marginal land.
Abbreviation | Description and Website | Duration | Consortium | Funding |
---|---|---|---|---|
BEE | Biomass energy Europe http://www.eu-bee.eu/ |
03/2008-11/2010 | 16 partners from Austria, Croatia, Finland, Germany, Greece, The Netherlands, North Macedonia, Poland, Sweden, Ukraine | EU research funding 2007-2013 7th framework programme (FP7) Overall budget: € 2 820 807 |
OPTIMA | Optimization of perennial grasses for biomass production http://www.optimafp7.eu/ |
10/2011 – 09/2015 | 21 partner from Belgium, Germany, Greece, Hungary, Ireland, Italy, The Netherlands, Portugal, Spain, The United Kingdom, and SICA members (Argentina, China, India) | EU research funding FP7 + Central American Integration System (SICA) Overall budget: € 3 913 249,84 |
WATBIO | Developing drought-tolerant biomass crops for Europe (poplar, miscanthus and Arundo donax L.) http://www.watbio.eu/ |
11/2012-10/2017 | 22 partners from France, Germany, Greece, Italy, The Netherlands, Spain, Sweden, The United Kingdom | EU research funding FP7-KBBE (knowledge-based bio-economy) Overall budget: € 11 660 401,40 |
FORBIO | Sustainable bioenergy production potential on available underutilized lands in Europe https://forbio-project.eu/ |
01/2016 -12/2018 | 12 partners from Belgium, Germany, Hungary, Italy, Ireland, Poland, Romania, Ukraine, The United Kingdom | EU programme Horizon2020 € 1 941 581 |
SEEMLA | Sustainable exploitation of biomass for bioenergy from marginal lands http://seemla.eu/ |
01/2016 -12/2018 | 8 partners from Germany, Greece, Italy, Ukraine | EU programme Horizon2020 € 1 629 884 |
MAGIC | Marginal lands for growing industrial crops http://magic-h2020.eu/ |
07/2017-06/2021 | 26 partners from Austria, France, Germany, Greece, Italy, Latvia, The Netherlands, Poland, The Portugal, Spain, Ukraine, The United Kingdom | EU programme Horizon2020 € 5 999 987,50 |
New-C-Land | Developing marginal land by producing plant biomass used for energy and materials https://www.newcland.eu/ |
01/2018-12/2021 | 9 partners from Belgium and France | Interreg France-Wallonie-Vlaanderen, co-financed by the European Regional Development Fund Overall budget: € 1 915 532 |
In many countries in sub-Saharan Africa, connecting the national electricity grid is highly expensive because their populated regions are spread over vast areas. In this context, decentralized renewable energy production from DEC cultivated on marginal lands offer an attractive solution [52]. The Crassulacean acid metabolism is a photosynthetic adaptation that facilitates carbon dioxide uptake at night and allows prickly pear (Opuntia ficus-indica (L.) Mill.) from Cactaceae family and African milkbush (Euphorbia tirucalli L.) to grow under arid and semi-arid climates and produce biomass for methane yield of 1860 m3 and 1791 m3 per 1 ha of marginal land respectively [52].
Another approach in sustainable energy crop cultivation is the development of integrated crop rotation that offers the supply with food and feed, the production of raw materials and energy sources such as biogas and the maintenance and further promotion of a multifaceted arable landscape [24]. For the development of sustainable crop rotation, experiments [24] elucidated optimum time of harvesting and methane yield in the cultivation of maize, winter wheat, triticale, winter rye, sunflower and grasses varieties. The highest methane yields of 7500-10200 m3N ha-1 were achieved from maize varieties, and the other crops resulted in 2-4 lower methane yields.
In an integrated crop rotation systems catch crops are plants that have short growth periods and can be cultivated between the vegetation periods of the main crops, thus increasing the efficiency of cultivation with regard to limited water and land resources. In this way, summer catch crops in Europe grow from June to October, and winter ones - from October to April [31]. Sorghum is a fast-growing crop with a shorter growth period compared to maize. It is characterized by wide adaptability to different environmental conditions and can be used as a summer crop [31, 40]. Sorghum is drought resistant due to the ability to delay reproductive development and a dense and prolific root system that is capable of extracting soil water deep in the soil profile, the ability to maintain stomatal opening at low levels of leaf water potential through osmotic adjustment [40, 53, 54].
The extensive study [26] was dedicated to energy crop combinations to produce biomass for biogas in reduced territories using double-cropping systems comparing to single crop: varieties of triticale, rye, and grass species as autumn-winter crops as well as varieties of sorghum and maize hybrids as spring-summer crops. In the single crop test, the fresh matter production per hectare was the highest in the case of sorghum (122.5 ± 10 Mg ha-1) owing to double harvest, but in DM yield context, the most efficient were maize and sorghum (17.6-21.5 Mg DM ha-1). Crop successions increased fresh and DM production from the territory as well as the biogas yield. Maize by itself resulted in up to 12 969 ± 812 Nm3 ha-1 biogas, and the most productive combination was triticale + maize with 18 737 ± 2357 Nm3 ha-1 of biogas. The biomass and biogas outputs in the research performed in Italy [26] were 15-20% higher in comparison to other reports from Austria [24], Germany [27], and Finland [25] due to the soil fertility and climate conditions.
Thereby, the cultivation of DEC brought new farming practices and new crop rotation systems, where intercropping and combined crop cultivation are the subjects of intensive research [5]. Further research is however required to ensure that the land-use change implications are well understood and the cultivation of energy crops is not detrimental to other land use or associated water resources, particularly for food production [17].
2.2. Agricultural Residues
Agricultural crop residues are one of the main concerns of the farming industry and are known to be significant contributors to GHG generation [55]. According to the definitions [48], primary agricultural residues are materials which remain in fields as by-products after the primary product of crops has been harvested (include cereal grain straws, wheat (Triticum), barley, rice (Oryza), corn stovers, stalks, leaves, etc.); and secondary agricultural residues arise during the processing of agricultural products for food or feed production (such as bagasse, sunflower husks, nutshells and so on). When using agricultural residues for biogas production, two sustainability issues should be considered: the potential competition with feeding in animal husbandry and possible depletion of organic matter in the soil and nutrients in agricultural lands because of the removal of straw from fields [48].
Some lignocellulose biomass has high lignin content which results in a slow and incomplete anaerobic fermentation [30, 55]. Plant materials may also contain a high percentage of carbon so the C/N ratio is too high [6]. In such cases, co-digestion with other substrates is more preferable than mono-digestion [6, 55]. On the other hand, the high content of water and the high fraction of fibers in manure cause low biogas yield typically ranging from 10 to 20 m3/t whereas the operation is considered profitable when biogas yields higher than 30 m3/t of treated material are achieved [56, 57]. To increase the biogas yield, a co-digestion with crop residues can be introduced. Thus, the addition of 4.6 kg of wheat straw (240 m3 CH4 per 1 t straw) to 1 t of swine manure resulted in a 10% methane production increase [57]. Biogas and methane potentials of some plant residues are comparable to energy crops on a dry weight basis (Table 3).
Biodegradable solid waste | Biogas obtainable on batch digestion (L kg−1, dry weight) | Methane in biogas, % |
Banana (fruit and stem) | 940 | 53 |
Potato (tuber) | 880 | 54 |
Sugar beet (root) | 620 | 65 |
Sugar beet (leaves) | 380 | 66 |
Grass | 450–530 | 55–57 |
Maize (whole plant) | 350–500 | 50 |
Oats (whole plant) | 450–480 | 51–55 |
Hay | 350–460 | 54–65 |
Straw (ground) | 350–450 | 54–58 |
Straw (chapped) | 250–350 | 58 |
Water hyacinth | 400–420 | 56 |
Salvinia | 430–480 | 58 |
2.3. Wastes
A rapid increase in the global population is leading to an increased demand for living resources such as food, feed, and fuel and, at the same time, to the generation of a large amount of wastes [58]. Improper management of organic waste can act as a major contributor to multifold environmental problems, such as climate change, ecosystem damage and resource depletion [59].
2.3.1. Food Waste
Approximately, one-third of all food produced for human consumption worldwide is discarded as waste, representing about 1.3 billion tons of waste per year [58]. It was elucidated [60] that AD of wastes prevents the spread of pathogens and environmental degradation caused by the wastes when those are allowed to runoff water basins and drain into the oceans. A few examples are provided here which illustrate the potential of biogas technology implemented in the treatment of plant processing food waste.
A coastal city of Turkey Giresun manufactures about 13.54% of world hazelnut (Corylus) turnover but pours organic wastes of this production into the sea [61]. It was evaluated at Giresun University [61] that the annual biogas production potential of Giresun city in anaerobic fermentation of hazelnut shells and wastes is 38.21 GWh.
AD has been found to be a better option than thermal technologies for bakery such as waste bread, biscuits, donuts, pizza dough waste, etc [62]. Bakery waste is an unsold and off-test food of cereal origin undergone inspection for visible mold, bacterial infection, and contaminations [63] though it stores mold when accumulated and not utilized [64]. The literature review indicated [62] that bakery waste produced 45-61% methane at 20-40 °C, in pH range from 5.3 to 7.4, with retention time from 12 to 55 days. Bakery waste contains easily degradable carbohydrates, enriched in vitamins [63] and can be considered a good co-substrate for fruit, vegetable and agricultural waste as it increases methane production [62].
2.3.2. Industrial Wastewaters
Implementation of anaerobic technologies in the world started with wastewater treatment [10, 11]. Industrial wastewater is one of the major sources of aquatic pollution which could significantly endanger surrounding environments and ecosystems [65]. AD has several advantages compared to aerobic wastewater treatment including the production of renewable energy, mainly in a form of biogas, substantially lower energy requirement, and less sludge to dispose of [65].
Among liquid wastes of plant feedstock processing, the potential of brewery wastewater [66-70], cassava (Mánihot esculénta Crantz) starch wastewater [71-74], palm oil mill effluent [75-83], biodiesel wastewater [84-87], and bioethanol wastewater (vinasse) [88-102] have attracted a lot of attention [65].
Vinasse (sugar beet (Beta vulgaris L.) of sugarcane (Saccharum) molasses stillage), a brown liquid with an unpleasant odour, is the main residue of alcohol production and is generated in distillation step in volumes between 8 and 15 liters per liter of ethanol obtained [65, 88, 95]. According to the State Statistics Service of Ukraine, in 2018, 333 850 tons of beet vinasse was poured on the fields of filtration in Ukraine polluting air and land, which resulted in growing CO2 emissions and deteriorating people’s living conditions. The beet vinasse characteristics are shown in Table 4.
Parameters* | Value | Macroelements** | Value | Microelements** | Value |
---|---|---|---|---|---|
DM, g kg-1 | 600-808 | Ca, g 100 g-1 | 0.04 | Al, mg kg-1 | 0.21 |
VS, g kg-1 | 408-598 | K, g 100 g-1 | 1.12 | As, mg kg-1 | <0.1 |
Total ammoniacal nitrogen, g l-1 | 1-6 | Mg, g 100 g-1 | 0.005 | Be, mg kg-1 | <0.5 |
Total Kjeldahl nitrogen, g l-1 | 23-38 | Na, g 100 g-1 | 0.28 | Bi, mg kg-1 | <0.5 |
Crude protein, % in VS | 30-37 | P, g 100 g-1 | 0.013 | B, mg kg-1 | 2.39 |
pH | 5.0-5.6 | S, g 100 g-1 | 0.176 | Cd, mg kg-1 | <0.1 |
Chemical oxygen demand (COD), g l-1 | 395-582 | Co, mg kg-1 | <0.5 | ||
Carbon, g l-1 | 158-203 | Cr, mg kg-1 | <0.1 | ||
C/N ratio | 5.9-6.0 | Cu, mg kg-1 | 0.41 | ||
Acetic acid, g l-1 | 15-20 | Fe, mg kg-1 | 15.32 | ||
Propionic acid, g l-1 | 0.13-0.17 | Li, mg kg-1 | 0.12 | ||
Iso butyric acid, g l-1 | 0.00 | Mn, mg kg-1 | 9.75 | ||
Butiric acid, g l-1 | 0.06-0.20 | Mo, mg kg-1 | 0.10 | ||
Iso valeric acid, g l-1 | 0.04-0.21 | Ni, mg kg-1 | 0.66 | ||
Valeric acid, g l-1 | 0.00 | Pb, mg kg-1 | <0.1 | ||
Total volatile fatty acids (VFA), g l-1 | 16-20 | Sb, mg kg-1 | <0.5 | ||
Sr, mg kg-1 | 2.68 | ||||
Ti, mg kg-1 | <0.5 |
**Diluted beet vinasse.
AD is one of the most promising technologies to treat ethanol wastewater as the methane produced can be used as an energy source in ethanol production plants [65]. However, the use of vinasse for methane fermentation requires a co-substrate to be added due to the low C/N ratio (about 6) and low content of macro- and microelements (Table 4) [90]. One of the approaches to overcome this obstacle may be adding lignocellulosic biomass. To achieve maximum biogas production by fermentation, an optimal ratio of vinasse to lignocellulosic biomass has to be determined. An experimental facility project for biogas fermentation of complex substrates consisting of vinasse and lignocellulose biomass has been developed according to the proposal by the Institute of Food Biotechnology and Genomics, NAS of Ukraine for the company “Eco-Energy” (Sumska region, Ukraine). Sweet sorghum bagasse and vinasse are produced by the company “Eco-Energy” as by-products from bioethanol production. Sweet sorghum bagasse is gained after plant stem crushing to obtain sweet sorghum juice as a source of sugars for bioethanol production. Fermentation is expected to be performed under thermophilic conditions because the main substrate vinasse is obtained at an initial temperature of 70 °C. Input components are 500 t/day vinasse with about 11% DM and 30 t/day shredded sorghum bagasse with about 90% DM. The process of fermentation occurs in concrete continuously stirred tank reactors (CSTR) with recirculation of the microorganisms. The calculated output is 2 500 nm3/day biogas (for heat and electricity) and 510 t/day of digestate for crop fertilisation.
3. PROCESS DESIGN
3.1. Parameters of Anaerobic Fermentation
AD and biogas production depends on many important parameters (Table 5) including temperature, pH, substrate DM rate, Organic Dry Matter (ODM) rate, C/N ratio, Hydraulic Retention Time (HRT), and Organic Loading Rate (OLR) [12, 61].
Different species of methanogenic bacteria function optimally in peculiar temperature ranges: psychrophilic, mesophilic, and thermophilic [6]. Higher temperature significantly improves the microbial growth kinetics, enzymes secretion, substrate diffusion, and mixing but affects the gas solubility, influencing the sulfide and ammonia toxicity, especially to methanogens [12]. Although the thermophilic process is generally the most efficient, large-scale AD is frequently carried out under the mesophilic conditions which are much easier to control and require less energy for heating [6, 12]. Moreover, the thermophilic process needs to be well buffered as it has a higher VFA/alkalinity ratio [12].
The pH is one of the most important operational parameters due to a wide range of optimal pH for particular microbial groups in the AD process: 5.5-6.5 for hydrolysis and acidogenesis as well as 7.8-8.2 for methanogenesis, therefore, neutral pH 6.8-7.4 is fitted for mixed culture if the whole process is performed in one digester [12].
Parameters | Optimal Range |
---|---|
Temperature, °C | Mesophilic: 30-42 Thermophilic: 48-55 |
pH | 6.8-7.4 |
C:N ratio | 10-40 |
Total solids | Liquid-state: <15% Solid-state: 15-40% |
Solids retention time (SRT) to hydraulic retention time (HRT) ratio | » 1 |
Total VFA (mg/l as acetic acid) | 50-250 |
Acetic acid (mg/l) | < 1000 |
Propionic acid (mg/l) | < 250 |
COD to nitrogen to phosphorus | 350:7:1 |
Retention Time (RT) is the duration for the substrate and microorganisms to be kept together in a digester to achieve the desired extent of degradation [6]. Accordingly, HRT (or substrate retention time) is the time that an organic material stays in a digester from the moment it is added into the digester to the time of its evacuation [6]. In practice, HRT may last from a few hours in case of easily degradable soluble wastes up to several months in case of energy crop digestion [34]. For the efficient anaerobic fermentation, solid (microorganisms) retention time to HRT ratio should be more than 1 [12]. The shorter SRT the smaller would be the size of the reactor which accounts for 70-80% of the process total cost, and microorganism retention time, on the contrary, should be maximized [6]. In reactor configurations with biomass retention/recycling, the time microbes are retained in the bioreactors is much longer than the time a soluble substrate was kept resulting in a low substrate retention time without biomass washout [12].
RT and HRT are tightly connected with the OLR, the amount of ODM to be injected in the reactor. Substrate properties such as concentration and degradability, milieu parameters (e.g., temperature, pH), and the reactor performance (configuration, mass transfer capability, scum and bottom layer formation, etc.) determine the maximum allowable loading rate [34]. Depending on the influential factors listed, volumetric loadings for the same substrate can vary in the range between 5-40 gI-1d-1 VS [34]. It is important to avoid overloading or inadequate mixing of substrates which can cause a significant rise in VFA concentration, a sharp drop in pH and system failure [6, 12]. This is the reason for the concentration of total VFA under control (Table 5).
A properly balanced nutrient composition must be provided in the substrate for stable fermentation [12, 34]. The performance of digesters fed with nutrient-deficient substrates such as lignocellulosic feedstock can be greatly improved by co-digestion with nutrient-rich substrates such as food waste or animal manure [12]. The carbon to nitrogen ratio is one of the crucial substrate properties in AD. The high C/N ratio results in VFA accumulation [65], besides, the nitrogen is consumed rapidly by the methanogens to meet their protein requirements and is no longer available to react on the left-over carbon content in the material, and both circumstances may inhibit biogas production [6]. If the C/N ratio is too low, nitrogen is liberated and accumulates in the form of ammonia/ammonium which consequently increases the pH of the material and inhibits AD as well [6, 104]. Hence, a higher C/N ratio leads to a higher methane production but it lowers buffer capacity, while a low C/N ratio decreases methane production, increases the buffer capacity. To balance the C/N a correlation co-digestion strategy can be applied [104]. In addition, supplementing trace elements, particularly iron, nickel, cobalt, molybdenum, selenium, magnesium, zinc, manganese has been shown to have a positive effect on the stability of the AD process and methane production [12].
Inhibiting or toxic components of the substrate can cause retarded methane formation, a decrease of the methane content in biogas or even complete failure of methanogenesis [34]. Inhibition has been reported to occur from long-chain fatty acids such as oleate and stearate, antibiotics, phenols, organic solvents, e.g., chloroform, and higher levels of heavy metals [6, 34]. However, gradual adaptation to increased levels of inhibitory substances or complete degradation/detoxification can be observed for some toxic components such as pentachlorphenol, nitroaromatic compounds, chlorinated aliphatic or aromatic hydrocarbons, and azo dyes [34].
Anaerobic microorganisms can also be inhibited by metabolic by-products generated during the fermentation, e.g., hydrogen, ammonia, sulphide, and VFA [34, 105]. The extensive review indicates [34] that maintenance of a low hydrogen partial pressure (1-10 Pa) regulates the degradation of propionate and butyrate. Besides, it also allows the acetate-utilizing methanogens to sustain the pH by conversion of acetic acid to methane and CO2. The increased partial pressure of hydrogen results in the accumulation of intermediate organic metabolites with subsequent pH drop below 6, ceasing methane generation [34]. Meanwhile, a competition for the available hydrogen can occur during methanogenesis, and sulphate-reducing bacteria obtain hydrogen and acetate more easily than methane-forming bacteria under low-acetate concentrations which increase sulphide levels and inhibit all reaction stages [34].
The destruction of organic matter, primarily the proteins [5, 34, 105] but also nitrates [34], releases ammonia nitrogen. As do sulphate reducers, nitrate-reducing bacteria compete successfully for the hydrogen normally used for CO2 reduction to methane, subsequently, substrates with high protein or nitrate contents may suppress methane formation and cause considerable ammonia toxicity during AD [34]. Increasing pH and temperature will lead to an increased fraction of free ammonia [5] that can penetrate the cell membrane [105]. Methanogenic bacteria are especially sensitive to the unionized molecules of ammonia [5, 105], sulphide, and VFA [105]. Some process parameters, such as temperature, retention time inside the digester, pH, etc., have a direct or indirect impact on the sanitation efficiency of the AD process [5]. However, there are feedstock types which require separate pre-sanitation process (pasteurization or pressure sterilization), e.g. wastewaters from slaughterhouses, food and catering wastes and flotation sludge [5].
The main target product of biogas production is methane; any other gasses contained in biogas are unwanted and are considered as biogas pollutants [103, 106]. Such components reduce the density, calorific value, and Wobbe index of biogas [106]. H2S and NH3 components in biogas are toxic and extremely corrosive, damaging the combined heat and power (CHP) unit and metal parts via emission of SO2 from combustion [106]. The relative content of CH4 and CO2 in biogas mainly depends on the nature of the substrate and pH of the reactor, N2 appears from the dissolved air in the substrate, water vapours come from substrates at thermophilic temperatures, hydrogen sulfide recovers from substrate sulfates, and ammonia originates from the degradation of nitrogen-containing compounds such as protein, urea, and uric acid [103, 106]. To remove unwanted compounds, various biogas upgrading methods are commercialized; the major ones are water scrubbing, chemical adsorption, pressure swing absorption, membrane and cryogenic separation [107].
3.2. Substrate Utilization
The composition and digestibility of substrates are the most important parameters in methane yield [61]. It is determining for the structure and the composition of biogas substrates that an increasing amount of lignin is deposited into the cell walls in the process of plant crop growth to ensure their stability [30]. Lignin is a strongly cross-linked hydrophobic three-dimensional polymer consisting of three primarily monolignols (p-coumaryl, coniferyl, and sinapyl alcohols) with amorphous structure resistant to microbial degradation [30, 108, 109]. The lignin content and composition varies among species, phylogenetic groups, cell types, and developmental stages of plants [109]. Most studies on specific methane yield prediction provide linear or non-linear models across crops with lignin content as major regressor variable [36].
Cellulose is a fibrous water-insoluble linear polysaccharide, a homopolymer of glucose joined by β-1,4 linkages [110]. Hemicelluloses are branched polysaccharides composed of pentoses (arabinose, xylose), hexoses (galactose, glucose, mannose) and acetylated sugars that serve as cement compounds between lignin and cellulose fibers in the united cell structure to form lignocellulosic complex [30, 108]. Hemicelluloses in agricultural biomass like straw and grasses are composed mainly of xylan that can be extracted easily in an acidic or alkaline milieu, whilst softwood hemicelluloses contain mainly glucomannan which requires a stronger alkaline milieu for extraction [108]. Since hemicellulose, unlike cellulose, has a lower molecular weight, is not crystalline but highly branched and amorphous, it has hydrophilic properties and is more easily accessible to hydrolytic enzymes for microbiological degradation than cellulose and lignin [30, 108].
Due to the strong integration of lignin, an increase of lignin content makes the lignocellulosic complex more resistant to biochemical degradation, and hydrolysis is the limiting step in methane fermentation of lignocellulose [30]. Since plant biomass contains in general 40-50% cellulose, 20-40% hemicellulose, and 20-30% lignin in DM, consequently, its characteristics such as lignin content, cellulose accessibility to cellulase, and cellulose crystallinity to a large extent determine the overall digestibility of the plant feedstock [108]. Although hemicelluloses, being lignocellulosic components, are highly thermo-chemically sensitive, severity parameters must be carefully optimized to avoid the formation of hemicellulose decay products such as furfurals and hydroxymethyl furfurals, which have been reported to inhibit the microbiological fermentation process. Such inhibition is more pronounced in aerobic conditions than in anaerobic [108, 111, 112]. In the fermentation of lignocellulosic hydrolysates, phenolic compounds have also been suggested to exert a considerable inhibitory effect with low molecular weight compounds being the most toxic [112]. At the same time, the inhibition of the third phase of anaerobic fermentation, acetogenesis, in lignocellulosic substrates is rather unlikely to happen due to the slow-running previous phases of hydrolysis and acidogenesis which prevent the accumulation of organic acids [30].
Pectins, proteins and the low-structure carbohydrates such as sugar and starch can be easily attacked by microorganisms and decomposed relatively quickly [30]. The overall scheme of organic constituents’ anaerobic degradability is illustrated in Fig. (2).
If the elemental composition of a substrate is known, the theoretical biogas yield can be calculated on the basis of the stoichiometric reaction. In methane fermentation of glucose the formula will be as follows [34]:
C6H12O6 = 3 CH4 + 3 CO2
As a result, under standard conditions, 1 mole of the carbohydrate glucose gives 3 moles of methane and 3 moles of carbon dioxide, or 134.4 l biogas out of 180 g glucose (0.747 l/g) [34]. Similarly, the theoretical biogas yield from lipids and proteins will be 1.25 l/g (32% CO2 + 68% CH4) and 0.7 l/g (29% CO2 and 71% CH4) correspondingly [34].
Theoretical expectations that oil plants, due to the high content of lipids, should attain particularly high specific methane yields, are not supported by empirical studies [113]. For instance, oil crop sunflower (Helianthus annuus L.) produced substantially lower specific methane yields than maize [113]. It is known [34, 114] that long-chain fatty acids and higher oil concentrations can inhibit the anaerobic fermentation, though as shown in the study [115], in some cases adding a small amount of oil may significantly increase biogas yield.
A plant biomass-based renewable energy research has recently turned towards the investigation of quick and reliable valuation methods to determine the substrate quality of plant biomass for biogas processing which enables biogas plant owners to optimize the substrate production and purchase [36]. A laboratory procedure has been invented at the University of Hohenheim to determine the quantity and quality of biogas, e.g., methane gained as a result of an organic break-down of substrate samples less than 5 g of dry biomass in a batch process [116].
3.3. Biomass Treatment
The substrate quality of plant biomass for biogas processing widely varies not only depending on the plant species but also concerning management practices [32, 36]. Biomass treatment of plant crops for biogas production consists of cultivation, harvesting, transportation, storage, pretreatment, configuration/control of the anaerobic process, treatment, storage and use of digestate [29, 117].
The time of crop harvest can influence the composition of the ingredients regarding the methane yield [29, 30]. In the case of grasses, late harvest leads to higher lignin content causing slowing down and decreasing methane yield [29]. Although Miscanthus × giganteus cultivated for combustion purposes is harvested after winter when lignin and DM contents are high, for biogas plants and improved digestibility it is necessary to harvest miscanthus green, before winter [118]. The silage quality is better when miscanthus is harvested in mid-October due to the highest lactic acid content (average: 3.0% of DM) and the lowest pH (average: 4.39) compared to the harvests in mid-September and beginning of October [119]. On the contrary, late hybrids of maize, compared to medium-early hybrids, attained the highest specific methane yield and maximum methane hectare yields at the final harvest date taking full advantage of the growing season and providing higher whole-plant DM concentration [113]. Consequently, maize for biogas is recommended to harvest later than the forage maize.
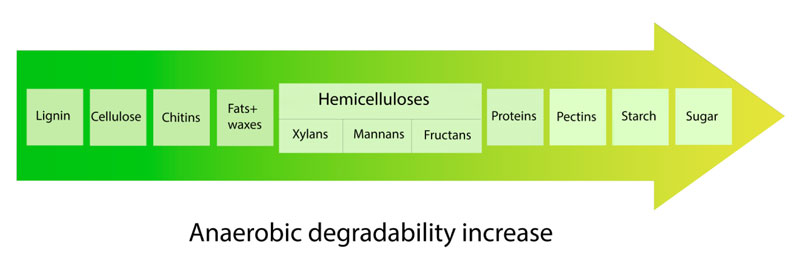
Biomass storage serves to compensate for the seasonal fluctuations of feedstock supply and to facilitate mixing different co-substrates for non-interrupted uploading to the digester [5]. Solid feedstock can be stored as shown in Fig. (3) in large heaps on the ground or in bunker silos and require pressing by tractor or covering to minimize aerobic reactions and undesired gas emissions [5, 120].
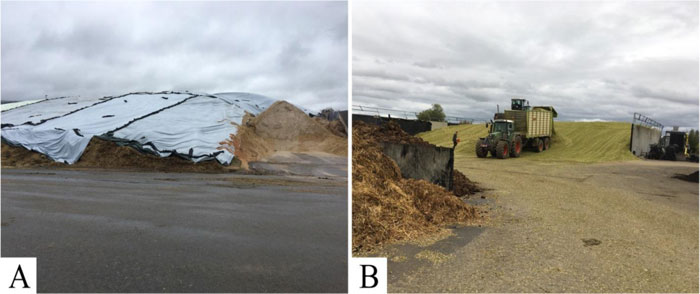
According to the general principle of organization of protective measures in biogas technology, which states that the formation of hazardous gases outside the feeding system must be minimized, mixing of substrates outside closed tanks should be avoided to prevent chemical reactions and formation of hazardous gases, such as hydrogen sulfide, carbon dioxide or ammonia [103].
3.3.1. Pretreatment Strategies
Some substrates contain chemicals that inhibit the growth and activity of the microorganisms or create physical obstacles like floating, foaming or clumping, block impellors and pipes in biogas plants. The molecular structure of other chemicals is poorly accessible to microorganisms and their enzymes, for instance, because of their highly crystalline structure or low surface area [121]. However, the major drawback in AD is the lengthy process due to its distinct sequential steps (hydrolysis, acidogenesis, acetogenesis, and methanogenesis). The hydrolysis is the most rate-limiting factor for the entire process [104]. To make the AD fast and efficient for an extended variety of substrates various pretreatment technologies have been developed: physical (mechanical, thermal, ultrasound, electrochemical), chemical (alkali, acid, oxidative), biological (microbiological, enzymatic), and combined processes (steam explosion, extrusion, thermochemical) [121].
Mechanical pretreatment makes pieces of substrate smaller or squeezes them to open the cellular structure, increasing the contact surface area of the biomass, reduces viscosity and floating layers appearing in digesters [121]. The optimal particle size depends on the substrate composition and parameters of digestion. In a study [122], methane yields from barley straw increased between 19.2% and 54.2% due to the particle size reduction from 5.0 to 0.5 cm; in case of wheat straw, reducing the size to 5.0 cm and 0.2 cm rose the methane yield from 56.6% to 83.5%; rice straw and maize stalks did not show any significant methane yield improvement after mechanical pre-treatment.
As lignin undergoes no hydrolysis under anaerobic conditions, and cellulose/hemicellulose hydrolysis goes very long, pretreatment technologies have been developed to enhance biogas production from lignocellulosic materials [61, 123]. Thus, the digestibility of reed (Poales) biomass improved remarkably after the steam explosion at 200 °C for 15 min, and consequently, the specific methane yield increased up to 89% [124]. Likewise, a steam explosion at 220 °C for 1 min resulted in 20% higher methane production compared to non-treated wheat straw. However, the more severe treatment decreased biodegradability possibly due to the formation of inhibitory compounds [123]. Thermal pretreatment at different temperatures was applied to influence anaerobic digestibility of hazelnut shells and wastes, and it was found [61] that thermal pretreatment at 60 °C resulted in the highest biogas yield.
Wood wastes and residues comprise almost 50% of a tree converted into the final products and include residues from tree felling and processing as well as discarded furniture and building materials [125]. Nevertheless, a high carbon-to-nitrogen ratio and high crystalline cellulosic structure reduce biogas yield efficiency from wood leftovers [126]. It was shown [125] that thermo-chemical NaOH pretreatment of eucalyptus wood chips increased methane yield by 38.5% compared to untreated chips. The disadvantages of thermo-chemical pretreatment are a large amount of chemical reagent needed, the necessity of pH adjustment together with costly maintenance of thermal conditions [127]. A new thermochemical pretreatment of corn in the stove and by a low-temperature fast pyrolysis with a carrier gas flow rate at 4 and 3 m3/hour enhanced methane production by 18.07% and 18.33% respectively [127].
In a study [128], biological pretreatment with complex microbial agents was used to pretreat corn straw at a temperature of about 20 °C to improve biodegradability and biogas production. The microbial complex included yeasts (Saccharomyces cerevisiae Meyen ex E.C. Hansen, Coccidioidesimmitis sp., and Hansenula anomala (E.C.Hansen) Syd. & P.Syd.), cellulolytic bacteria (Bacillus licheniformis (Weigmann, 1898) Chester, 1901, Pseudomonas sp., and Bacillus subtilis (Ehrenberg, 1835) Cohn, 1872) and fungus Pleurotus florida (Mont.) Singer together with the lactic acid bacteria of Lactobacillus deiliehii sp. The pretreatment lasted for 15 days and resulted in 33.07% more total biogas yield, 75.57% more methane yield [128].
3.3.2. Two-stage Digestion Approach
The AD can be conducted in two separate phases: acidogenesis (producing VFA) and methanogenesis (producing methane and carbon dioxide) [104, 129]. Phase separation can increase specific bioenergy production, substrate degradation rate, improve the process stability and reduce retention time due to maintaining optimal conditions for different microbial populations working in two phases with distinct nutrient, pH, and other requirements [104, 129, 130]. Also, operating of the reactor system in the AD of rye silage and barley straw mixture at different temperature regimes, thermophilic hydrolysis/acidogenesis phase and mesophilic methanization, increased the methane fraction in the biogas to 85% [130]. To obtain high calorific value biogas (77% of methane) in anaerobic fermentation of maize silage and a mixture of grass and maize silage, an increased pressure up to 9 bar on the second stage bioreactor was applied [129].
3.4. Anaerobic Digesters Design
There are multiple types of biogas digesters operating in the world: made of concrete, steel, brick or plastic, shaped like silos, troughs, basins or ponds, placed underground or on the surface [5]. The DM content of the digested substrate determines the design of a biogas plant and the type of digestion [5].
Historically, research on high-solids anaerobic fermentation was focused on the single charge (batch), non-mixed reactor concept, with recirculation of the effluent [6]. In non-mixed systems, the rate of gas production is much slower than in mixed systems, but this technology allows treating solid wastes in larger quantities and saving water [6]. An example of batch digesters is a “garage type” made of concrete, for the treatment of source separated biowaste from households, grass cuttings, and energy crops with 15-40% (TS) [5]. Instead of mechanical mixing, the leachate collected at the bottom of the reactor is either recirculated back to the top of the reactor or mixed with a fresh substrate prior to feeding into the reactor [12]. The temperature of the process and of percolation liquid is regulated by a built-in floor heating system and by a heat exchanger, a reservoir for the liquid [5].
Suspended growth anaerobic reactor includes CSTR, up-flow of anaerobic sludge blanket digesters, anaerobic contact reactors, anaerobic sequencing batch reactors, and anaerobic baffled reactors [12]. Due to simple design and operation as well as the ability to be fed with diverse feedstocks at various total solids content, CSTR is the most common reactor design for currently working biogas plants [12, 131].
Mixing is required for the most anaerobic reactor designs to combine the incoming material with the bacteria, to maintain pH of the fluid, temperature, and nutrients homogeneity, to facilitate the up-flow of gas bubbles as well as to prevent the formation of swimming layers and sediments [5, 6]. If the rate-limiting step throughout the startup duration is methanogenesis vigorous mixing is viewed [121] to be counterproductive, whereas high mixing is recommended if the rate-limiting step is hydrolysis. Stirring is applied using mechanical, hydraulic or pneumatic equipment [5].
To eliminate biomass stratification and inhomogeneity, the rotary digester concept was introduced [132-134]. In the rotating digester, substrate mixing is performed by raising the mineral component of biomass and methane-forming bacteria accumulating in the lower part of the digester and immersing the organic component accumulating in the upper part [133]. The digester is designed as a horizontal cylinder rotating around a horizontal axis, partially immersed in the liquid of the outer casing [132, 134].
Attached growth anaerobic reactor allows microorganisms to attach on to diversified inert media with high specific surface area and design for treating low total solids (< 5%) containing wastewaters [12]. The variants of this configuration include an anaerobic filter, expanded bed reactor, and fluidized bed reactor [12].
Large farm-scale co-digestion plants usually consist of several digester tanks, including one or several main digesters and post digesters [5]. The storage tanks for digestate serve also as post-digesters and should be covered with a gas-tight membrane [5].
CONCLUSION
AD is a widely explored and promising technology that can utilize a broad range of plant substrates. From 2009 to 2018, global biogas capacities have more than doubled and continue to grow nowadays. Germany and the USA are the largest biogas manufacturers whereas Asian countries are the leaders in the number of smaller biogas digesters. Methane fermentation occurs in nature and in the process of the organic matter decay in an oxygen-deprived milieu. To avoid GHG released into the atmosphere, biogas collecting facilities should be located within the closest possible vicinity to the existing garbage dumps. Waste management practice involving organic fraction separation in households and in the industry should be applied.
Plant feedstock including energy crops, agricultural residues, and industrial wastes, may play a decisive role in the production of biogas as a renewable energy source. Energy crops due to high yields, low nutrient and water requirements as well as low establishment costs can be cultivated on marginal lands thus eliminating controversies between DEC and food crops. The introduction of crop rotation systems for DEC cultivation can be advantageous for effective land use. It may also be beneficial to co-digest energy crops and lignocellulosic agricultural residues with wastes to maintain the nutrient composition, particularly C/N ratio. Vinasse (molasses stillage) is the main residue (by-product) of alcohol production generated in large volumes. The AD of vinasse can be improved by mixing it with a co-substrate with a higher C/N ratio and macro-/microelement content.
The most important parameters of AD and biogas production include temperature, pH, substrate DM rate, ODM rate, C/N ratio, HRT, and OLR. The composition, digestibility and biomass pretreatment of plant feedstock influence the yield of methane. Construction of biogas facilities is beneficial for environmental, economic, and social reasons.
LIST OF ABBREVIATIONS
BEE | = Biomass Energy Europe International Project |
BIOPLAT-EU | = Promoting Sustainable use of Underutilized Lands for Bioenergy Production Through a Web-based Platform for Europe Horizon2020 EU Project |
Bcm | = Billion Cubic Meters |
COD | = Chemical Oxygen Demand |
CSTR | = Continuously Stirred Tank Reactor |
DEC | = Dedicated Energy Crops |
DM | = Dry Matter |
FORBIO | = ‘Sustainable Bioenergy Production Potential on Available Underutilized Lands in Europe Horizon2020 EU Project |
FP7 | = 7th Framework European Research Funding Programme |
GHG | = Greenhouse Gas |
HRT | = Hydraulic (Substrate) Retention Time |
MAGIC | = Marginal Lands for Growing Industrial Crops Horizon2020 EU Project |
MISCOMAR | = Miscanthus Biomass Options for Contaminated and Marginal Land: Quality, Quantity and Soil Interactions International Project |
New-C-Land | = Developing Marginal Land by Producing Plant Biomass used for Energy and Materials International Project |
oDM | = Organic Dry Matter |
OPTIMA | = Optimization of Perennial Grasses for Biomass Production International Project |
OLR | = Organic Loading Rate |
RT | = Retention Time |
SEEMLA | = Sustainable Exploitation of Biomass for Bioenergy from Marginal Lands Horizon2020 EU Project |
SRT | = Solids (Microorganisms) Retention Time |
TS | = Total Solids |
VFA | = Volatile Fatty Acids |
VS | = Volatile Solids |
WATBIO | = Developing Drought-tolerant Biomass Crops for Europe International Project |
CONSENT FOR PUBLICATION
Not applicable.
FUNDING
This work was supported by the National Academy of Sciences of Ukraine (partially in the project No. 0118U005321 and partially in the project No. 0119U101434). T.S. Ivanova appreciates the funding received from the U.S.-Ukraine Foundation Biotechnology Initiative to participate “proBIOGAS International – Biogas engineering and operating training with plant visits” in Stuttgart and Southern Germany (September 24th – October 2nd, 2019), which was organized by the International Biogas and Bioenergy Centre of Competence Fachgruppe Biogas GmbH and the State Institute of Agricultural Engineering and Bioenergy, University of Hohenheim, Germany.
CONFLICT OF INTEREST
The authors declare no conflict of interest, financial or otherwise.
ACKNOWLEDGEMENTS
We acknowledge the suggestions of Dr. V. Kyrylenko (Institute of Food Biotechnology and Genomics, National Academy of Sciences of Ukraine, Kyiv) aimed to improve the language of the manuscript.